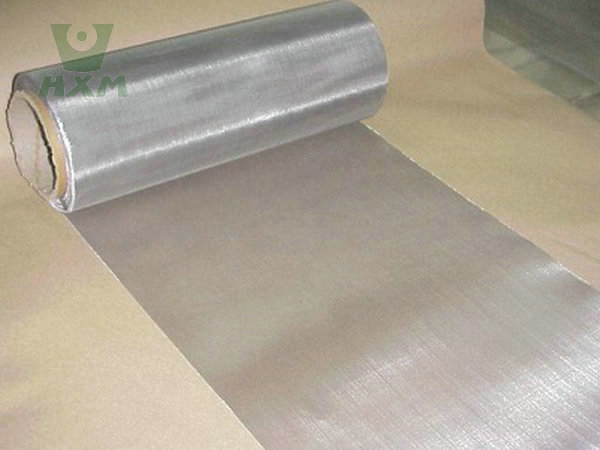
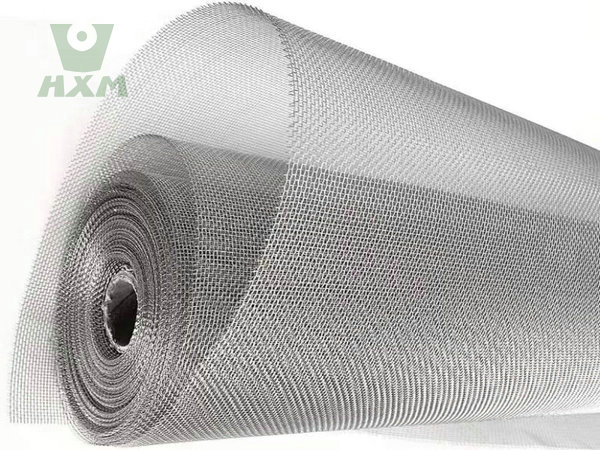
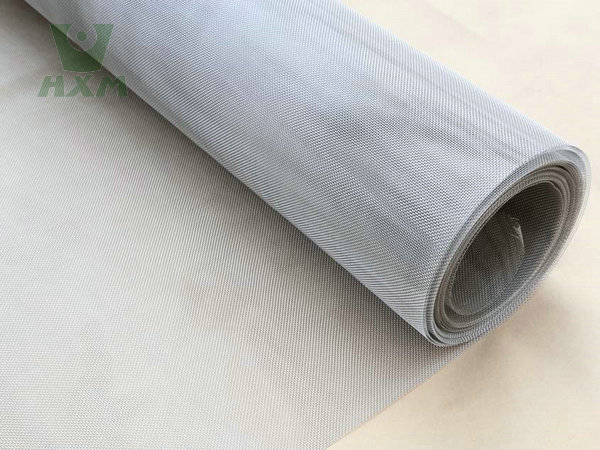
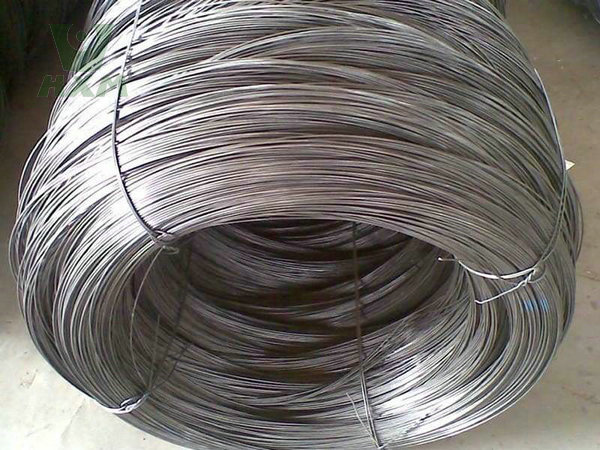
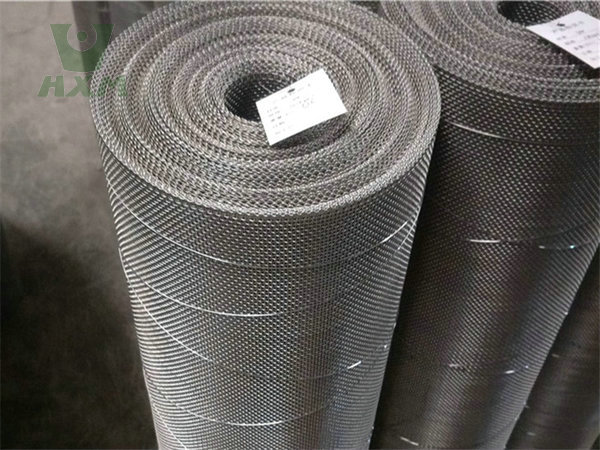
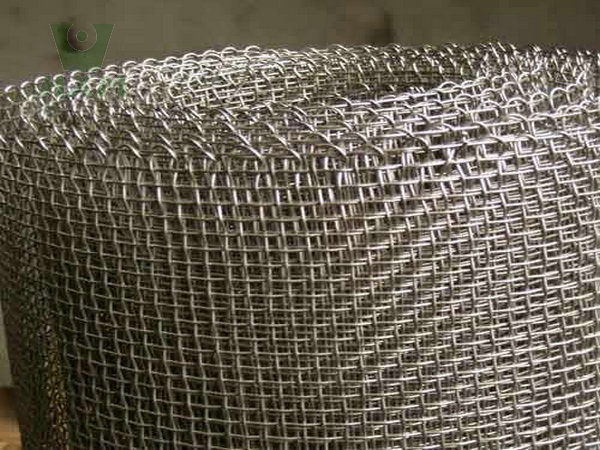
Hastelloy X Wire & Hastelloy X Mesh, please note that the above table, Huaxiao Metal Manufacturer provides a range of standard widths, and lengths for Hastelloy.
- Dimensions:
- Mesh : 2-200Mesh
- Diameter: 0.05mm-18mm
- Roll Width: 0.1m-1.5m
- Roll Length: 10-100m
*Customized size needs to be confirmed with us
- Delivery State: Cold Drawn, Hot Rolled, Forged, Grinding, Centerless Grinding
- Certification: ISO, SGS, BV and so on.
Composition of Hastelloy X Wire
Huaxiao Metal Supplier has the many kinds of hastelloy wire and hastelloy mesh, welcome to inquiry. Hastelloy X wire is a nickel-based high-temperature alloy with a well-balanced composition that provides excellent corrosion resistance, high-temperature strength, and good machinability. This makes it suitable for a wide range of applications in industries such as aerospace, chemical processing, and energy production.
Element | Range (%) | Role in Performance |
---|---|---|
Nickel (Ni) | Balance (~47%) | Base matrix; provides oxidation resistance & ductility. |
Chromium (Cr) | 20.5–23.0 | Forms Cr₂O₃ scale for high-temperature oxidation resistance (up to 2200°F/1200°C). |
Iron (Fe) | 17.0–20.0 | Lowers cost while stabilizing austenitic structure. |
Molybdenum (Mo) | 8.0–10.0 | Enhances strength at elevated temperatures & resists reducing acids. |
Cobalt (Co) | 0.5–2.5 | Boosts creep rupture strength in extreme heat. |
Tungsten (W) | 0.2–1.0 | Synergizes with Mo for solid-solution strengthening. |
We have a large amount of high-quality alloy inventory ready for shipment, please request a quote immediately.
Physical Property of Hastelloy X Mesh
Physical Property | Value |
---|---|
Density | 8.22 – 8.30 g/cm³ |
Melting Temperature Range | 1260 – 1355 °C |
Thermal Conductivity | ~14.4 W/m·K at 1000 °C |
Specific Heat Capacity | ~449 J/(kg·K) at 25 °C |
Electrical Resistivity | ~1.28×10⁻⁶ Ω·m at 20 °C |
Coefficient of Thermal Expansion | ~13.3×10⁻⁶ K⁻¹ at 20-100 °C |
Hastelloy X mesh exhibits a range of physical properties that make it suitable for various high-temperature and corrosion-resistant applications. Its high melting point, good thermal conductivity, high specific heat capacity, moderate electrical resistivity, and low coefficient of thermal expansion contribute to its overall performance in demanding environments.Huaxiao Metal Manufacturer provides the various the alloy products and the best solution for customers. Welcome to inquiry and ask for our exports any questions about alloy, we will all slove for you freely. Looking forward to your inquiry and email. We will reply and provide to you about your customerized solutions.
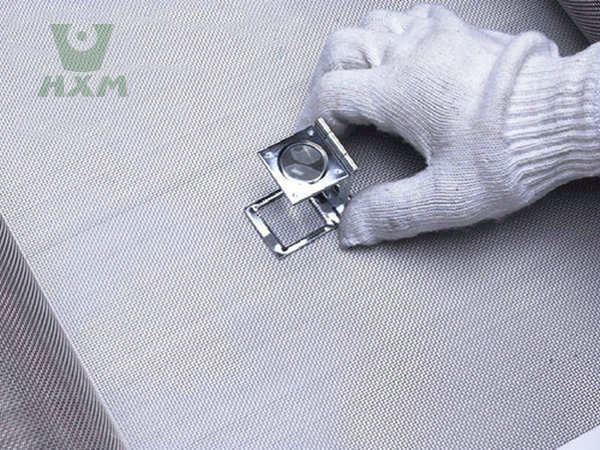
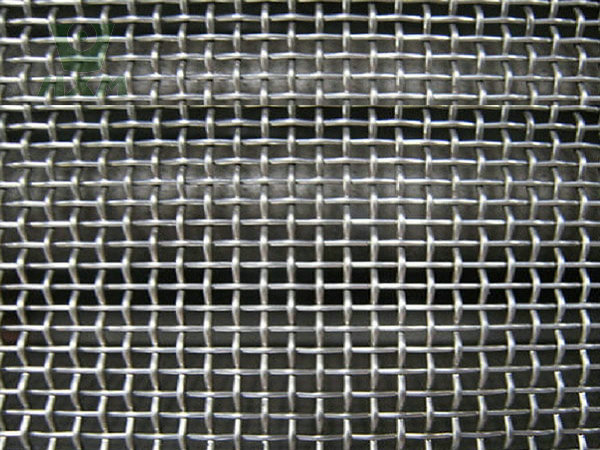
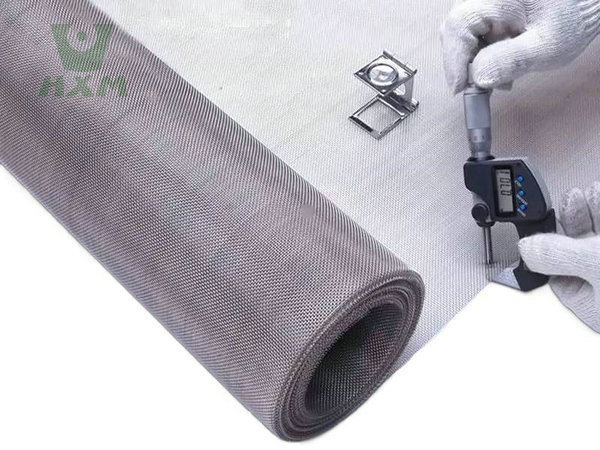
Mechanical Property of Hastelloy X Wire
Mechanical Property | Value |
---|---|
Tensile Strength (Ultimate Tensile Strength, UTS) | 730 – 950 MPa (Minimum 655 MPa, typically) |
Yield Strength (0.2% Offset Yield Strength) | 283 – 350 MPa (Minimum 240 MPa, typically) |
Elongation | 40% (Minimum 35%, typically) |
Hardness (Rockwell B) | Approximately 88 – 95 (depends on heat treatment and condition) |
Creep Resistance | Excellent at temperatures up to approximately 900 °C (short-term exposure to higher temperatures, up to 1080 °C, is also possible) |
Hastelloy X wire possesses a combination of excellent mechanical properties, including high tensile and yield strengths, good ductility, moderate hardness, and excellent creep resistance. These properties make it an ideal choice for various high-temperature and corrosion-resistant applications in industries such as aerospace, petrochemical, and nuclear energy. We have a large amount of high-quality alloy inventory ready for shipment, please request a quote immediately. If you have any demand for Hastelloy alloy wire mesh, please contact us by email, special specifications can be customized according to requirements.
Advantages of Hastelloy X Wire
Excellent High-Temperature Strength and Creep Resistance:
- Hastelloy X wire maintains its mechanical properties at elevated temperatures, withstanding creep deformation effectively. This makes it suitable for applications where components are exposed to high temperatures for prolonged periods, such as in aerospace engines and industrial furnaces.
Outstanding Corrosion Resistance:
- The alloy demonstrates robust resistance to a wide range of corrosive environments, including those containing chloride ions and acidic gases. This corrosion resistance is due to the formation of a protective oxide layer on the surface of the material, which shields it from further attack.
Good Weldability and Fabricability:
- Hastelloy X wire is relatively easy to weld and fabricate, allowing for the creation of complex shapes and structures. This makes it a versatile material for use in various applications, from piping systems to structural components.
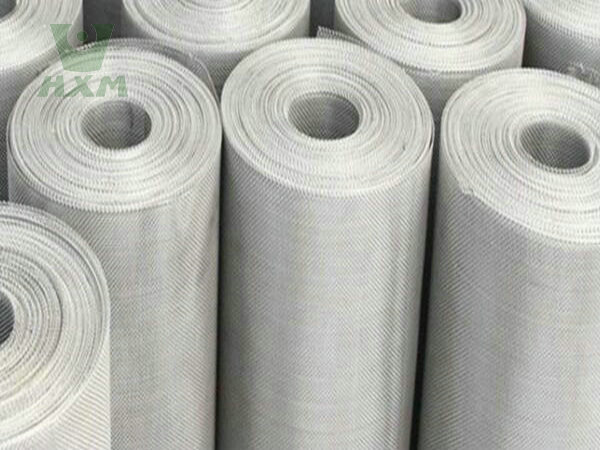
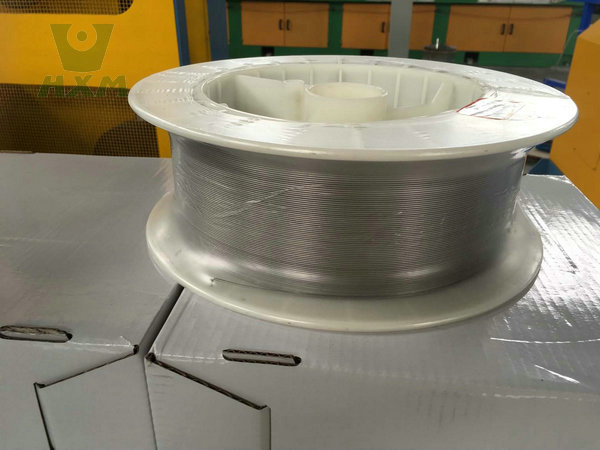
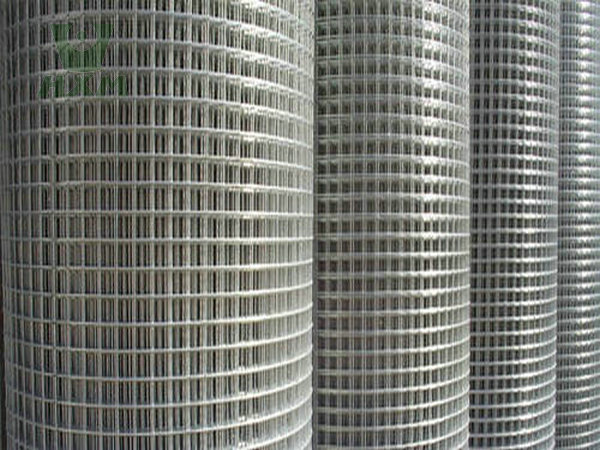
High Oxidation Resistance:
- The alloy forms a dense oxide layer at high temperatures, which protects the base material from oxidation. This resistance to oxidation extends the service life of components made from Hastelloy X wire in high-temperature environments.
Good Mechanical Properties at Room and Elevated Temperatures:
- In addition to its high-temperature strength, Hastelloy X wire also exhibits good mechanical properties at room temperature. This includes high tensile strength, yield strength, and ductility, which make it suitable for a wide range of applications.
Long Service Life and Reliability:
- Due to its combination of high-temperature strength, corrosion resistance, and good mechanical properties, Hastelloy X wire offers a long service life and high reliability in demanding applications. This reduces the need for frequent replacements and maintenance, lowering overall costs.
Hastelloy X wire is a highly advantageous material due to its excellent high-temperature strength, creep resistance, corrosion resistance, good weldability and fabricability, high oxidation resistance, and good mechanical properties at both room and elevated temperatures. These benefits make it an ideal choice for various applications in aerospace, petrochemical, nuclear energy, and other industries where high performance and reliability are critical.
Manufacturing Process of Hastelloy X Wire
The manufacturing process of Hastelloy X wire involves several crucial steps, each of which contributes to the final properties and quality of the material. Huaxiao Metal Supplier is professional and experienced in producing alloy products in China. Welcome to consult any question about alloy and contact us any time when you are free, and our company of stafff will reply you in 24 hours.
Alloy Composition
Hastelloy X is a nickel-chromium-iron-based superalloy, with a typical composition that includes:
- Nickel (Ni): Balance or remainder, providing the matrix for the alloy and contributing to its corrosion resistance and mechanical properties.
- Chromium (Cr): 20.5% to 23.5%, enhancing corrosion resistance and oxidation resistance.
- Iron (Fe): 17% to 20%, increasing mechanical strength and maintaining corrosion resistance.
- Molybdenum (Mo): 8.0% to 10.0%, improving high-temperature strength and corrosion resistance.
- Other elements such as cobalt (Co), tungsten (W), carbon (C), manganese (Mn), silicon (Si), aluminum (Al), boron (B), phosphorus (P), and sulfur (S) are present in smaller quantities, each contributing to specific properties of the alloy.
Melting and Casting
- Melting Techniques: The alloy is typically melted using vacuum induction melting (VIM) or vacuum arc remelting (VAR) to ensure high purity and minimize contamination.
- Casting: The molten alloy is then cast into ingots, which are subsequently hot-worked to improve their structure and properties.
Hot Working
- Temperature Range: Hot working of Hastelloy X is usually performed in the temperature range of 1050°C to 1150°C.
- Processes: Common hot working processes include hot rolling, forging, and extrusion. These processes enhance the ductility and workability of the alloy, allowing it to be shaped into wires and other forms.
Cold Working
- Processes: Cold working, such as cold drawing and cold rolling, can further refine the grain structure and improve the mechanical properties of Hastelloy X wire.
- Work Hardening: Cold working leads to work hardening, which may necessitate annealing or intermediate annealing to restore ductility.
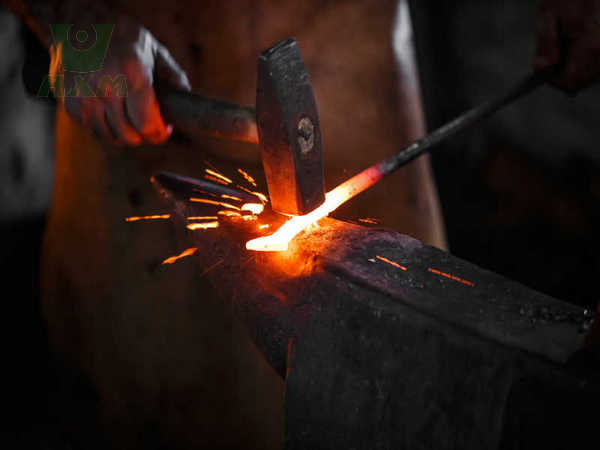
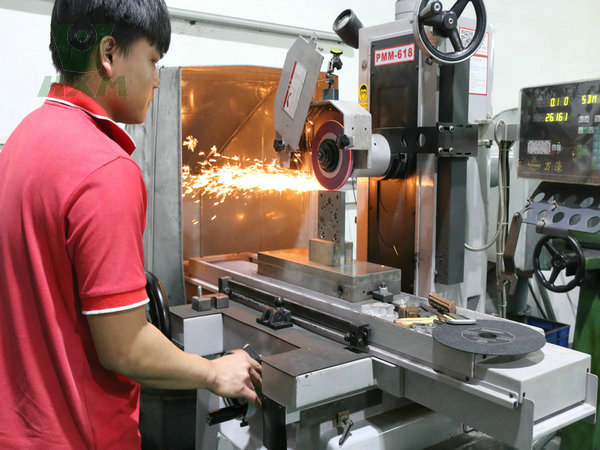
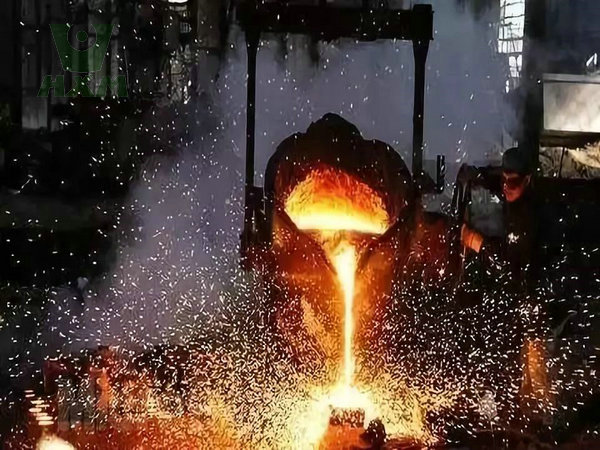
Heat Treatment
- Solution Treatment: This step is crucial for enhancing the high-temperature strength and corrosion resistance of Hastelloy X wire. The alloy is heated to a temperature between 1150°C and 1175°C (or 1175°C to 1225°C, depending on specific process parameters) and held for about 1 hour, followed by rapid cooling (water quenching or oil quenching).
- Aging Treatment: After solution treatment, aging at a temperature between 700°C and 800°C for 16 to 24 hours can further optimize the mechanical properties of the alloy.
Finishing and Inspection
- Surface Finishing: The wire may undergo surface treatments such as polishing or pickling to improve its appearance and corrosion resistance.
- Inspection: Rigorous inspections, including chemical analysis, mechanical testing, and non-destructive testing, ensure that the Hastelloy X wire meets the required specifications and standards.
Packaging and Shipping
- The final step involves packaging the Hastelloy X wire in a manner that protects it from damage during transportation and storage.
- Shipping documentation, including material certificates and test reports, accompanies each shipment to ensure traceability and compliance with customer requirements.
What is Hastelloy X Wire?
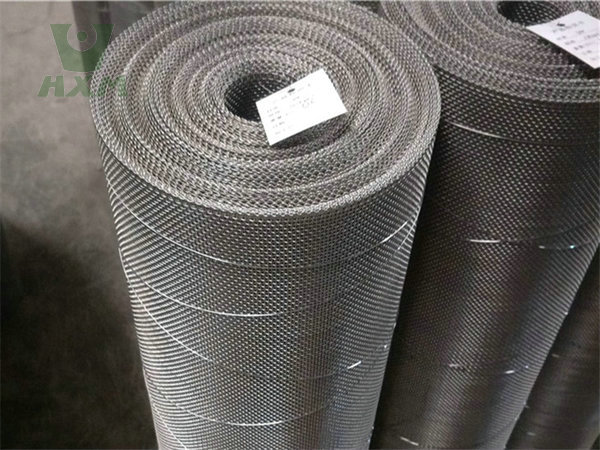
Hastelloy X Wire is a high-performance nickel-based alloy wire renowned for its exceptional high-temperature resistance, corrosion resistance, and mechanical properties. The specific composition may vary slightly depending on the manufacturer and application requirements, but typically, it contains a balance of nickel. Huaxiao Metal Supplier is professional and experienced in alloy producing factory, our company provides the personalized services and welcome to inquiry about the lastest price. As the distributer, our compoany has the most reasoanable policies for the alloy products.
Applications of Hastelloy X Mesh
Hastelloy X wire is a high-performance, corrosion-resistant alloy wire with excellent mechanical properties and high-temperature stability. Its unique composition and properties make it suitable for use in a wide range of industrial applications where corrosion resistance and durability are paramount. Welcome to ask for the lastest price.
- Aerospace: Components in jet engines, gas turbines, and rocket engines, such as turbine blades, nozzles, and combustion chambers, where high-temperature resistance and corrosion resistance are critical.
- Petrochemical: Equipment in refining and chemical processing plants, including reactors, heat exchangers, piping, and valves, that are exposed to high temperatures and corrosive media.
- Nuclear Energy: Components in nuclear reactors, such as cooling systems and structural parts, where resistance to high temperatures, radiation, and corrosion is essential.
- Automotive: High-performance engine components, particularly turbochargers and exhaust systems, where stability at high temperatures is required.
Why Choose Hastelloy X Wire?
The manufacturing of Hastelloy X Wire involves melting and casting the alloy, followed by hot and cold working processes to shape and refine the grain structure. Heat treatment, such as solution annealing and aging, further enhances the mechanical properties and corrosion resistance of the wire. Hastelloy X Wire is a versatile nickel-based alloy wire with exceptional high-temperature resistance, corrosion resistance, and mechanical properties, making it an ideal choice for various demanding applications across multiple industries.
China’s Top Supplier | Precision & Reliability
Certified Quality:AMS 5754 / ASTM B737 / GB/T 15007 compliant. Full traceability (MTRs), low S ≤0.003% for crack-free welds.
Extreme Performance: Unmatched oxidation resistance (1200°C), creep strength. Proven in C919 jet engines & Sinopec refineries.
Ready Stock, Fast Delivery: All diameters (0.1–8.0mm), spooled/straight. 48-hr China delivery; global DDP shipped.
Huaxiao Metal Manufacturer provides the hastelloy plate, and other shapes, such as tubes, wires, strip, coil, bar etc. Alloys of various shapes and materials are available, welcome to choose and consult the price.
Our products are guaranteed in quality, and our professional team can provide technical support and consulting services. If you need more information or have any questions, please free to contact our customer service team.
FAQ
Can you provide samples?
For small parts, we can provide free samples of regular sizes, but the shipping costs must be borne by you. For large samples, we will include it in the order amount. Please confirm with our sales department according to your specific requirements.
What is the functions of Hastelloy X wire?
Hastelloy X wire delivers exceptional high-temperature strength, oxidation resistance, and fabricability in extreme environments.Gas turbine combustion cans, aerospace seals, nuclear reactor hardware, and industrial heating systems.
Do you support customized sizes?
We provide various forms such as plates, rods, and pipes, with a minimum processing accuracy of ± 0.02mm. The customization cycle is usually 7-15 working days, and specific details need to be confirmed with the sales team.
How long is your delivery time?
It is usually 35 days, but it is also affected by your specific requirements or order quantity.
What is the minimum order quantity?
Our minimum order quantity is 100kg. Larger quantity, lower price.
How do you control product quality?
From raw material selection to packaging for transport, each production step undergoes rigorous testing and evaluation. Only products that pass all tests are approved for export.