The fabrication of Hastelloy corrosion resistant alloys involves various aspects, including material composition, properties, manufacturing processes, and applications. Below is a comprehensive analysis presented in both textual and tabular forms. Huaxiao Metal Supplier provides all kinds of hastelloy and welcome to inquire.
Overview of Hastelloy Corrosion Resistant Alloy Fabrication
Aspects | Details |
---|---|
Material Composition | Primarily Ni-Cr-Mo-based, with additions of Fe, Co, W, etc. |
Key Properties | Corrosion resistance, high temperature stability, stress corrosion cracking resistance |
Manufacturing Processes | Casting, forging, rolling, welding, machining |
Applications | Chemical industry, petroleum, aerospace, nuclear power |
Material Chemical Composition
Hastelloy corrosion resistant alloys are primarily composed of nickel (Ni), chromium (Cr), and molybdenum (Mo), with additional elements such as iron (Fe), cobalt (Co), and tungsten (W) in some grades. The specific composition varies depending on the alloy grade, but the primary elements provide the alloys with their corrosion resistance and high temperature stability. Huaxiao Metal Supplier is professional and experienced in producing the hastelloy in factory.
Hastelloy Alloy Grades and Characteristics
Hastelloy C276: This grade is widely used due to its excellent corrosion resistance in reducing environments, including those containing chloride ions. It has high nickel and molybdenum content, making it resistant to pitting and crevice corrosion.
Hastelloy B2: This grade is known for its resistance to hydrochloric acid and other non-oxidizing acids. It is suitable for applications involving high temperatures and corrosive media.
Hastelloy X: This grade is designed for high-temperature applications, with excellent mechanical properties and corrosion resistance up to 1200°C. It is commonly used in aerospace and industrial furnace components.
Hastelloy G30: This grade is specifically formulated for resistance to sulfuric and phosphoric acids, making it ideal for chemical processing equipment.
Hastelloy Alloy Advantages
Key Properties
- Corrosion Resistance: Hastelloy alloys exhibit excellent corrosion resistance in both oxidizing and moderately reducing environments. They can resist the attack of various acidic media and are particularly suitable for applications involving chloride ions and acidic gases.
- High Temperature Stability: These alloys maintain their mechanical properties and corrosion resistance at elevated temperatures, making them ideal for high-temperature applications.
- Stress Corrosion Cracking Resistance: Hastelloy alloys, especially grades like Hastelloy C, have excellent resistance to stress corrosion cracking (SCC), which is crucial for applications in harsh environments.
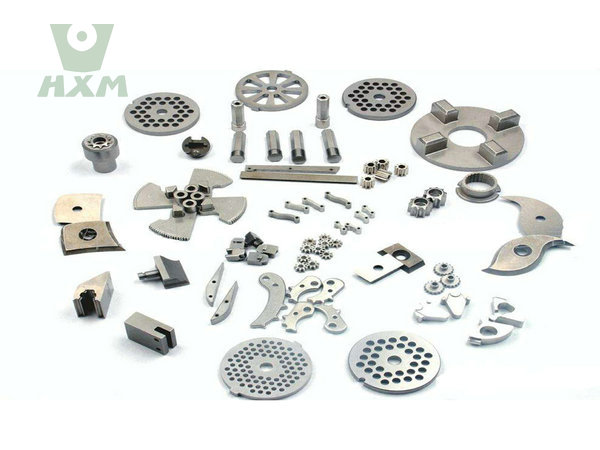
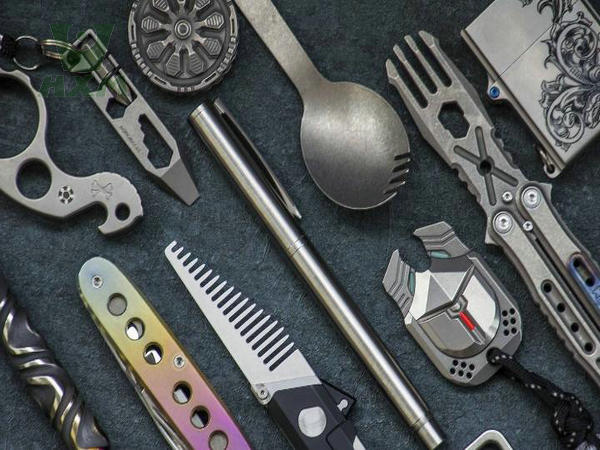
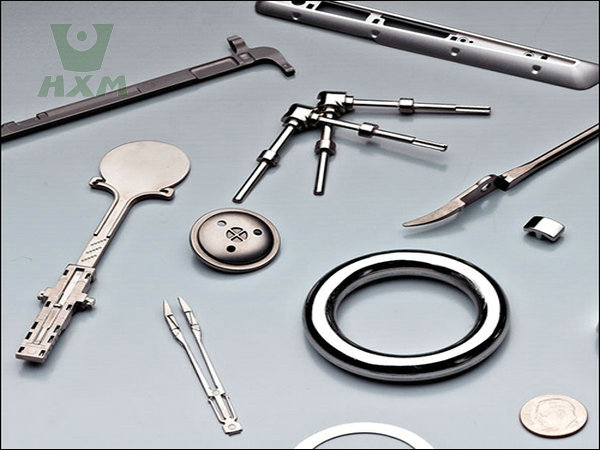
Advanced Manufacturing Techniques
The fabrication of Hastelloy alloys often requires specialized techniques to ensure optimal performance:
Electron Beam Welding (EBW): This welding process uses a high-velocity electron beam to melt and fuse the alloy materials. It produces narrow welds with low distortion and high corrosion resistance.
Powder Metallurgy (PM): This technique involves consolidating alloy powder particles into a solid form using heat and pressure. It allows for the production of complex shapes with uniform microstructure and enhanced properties.
Thermal Spraying: This process involves spraying molten alloy particles onto a substrate to form a protective coating. It is used to extend the service life of components by providing additional corrosion resistance.
Hastelloy Alloy Manufacturing Processes
The fabrication of Hastelloy corrosion resistant alloys involves several key processes:
- Casting: This process involves pouring molten alloy into molds to form shapes. It is suitable for producing large and complex components.
- Forging: Forging involves shaping the alloy by applying pressure and heat. It improves the mechanical properties and grain structure of the alloy.
- Rolling: Rolling is used to produce flat or cylindrical shapes by passing the alloy through rolls. It can be done at room temperature or elevated temperatures.
- Welding: Hastelloy alloys can be welded using various techniques, such as TIG, MIG, and plasma welding. Proper welding practices and post-weld heat treatment are essential to ensure the corrosion resistance of the welded joints.
- Machining: Machining processes such as milling, drilling, and turning are used to produce precision components from Hastelloy alloys.
Hastelloy Alloy Applications
Due to their excellent corrosion resistance, high temperature stability, and stress corrosion cracking resistance, Hastelloy alloys are widely used in various industries:
- Chemical Industry: Hastelloy alloys are used to manufacture reactors, distillation towers, heat exchangers, and other equipment that must resist the attack of various corrosive media.
- Petroleum Industry: These alloys are used in pipelines, valves, and other critical components in the oil and gas industry to ensure safe and reliable transportation of hydrocarbons.
- Aerospace: Hastelloy alloys are used in aircraft engines and other high-temperature components due to their excellent high-temperature stability and corrosion resistance.
- Nuclear Power: These alloys are used in nuclear reactors and other nuclear power equipment due to their ability to resist radiation and corrosion.
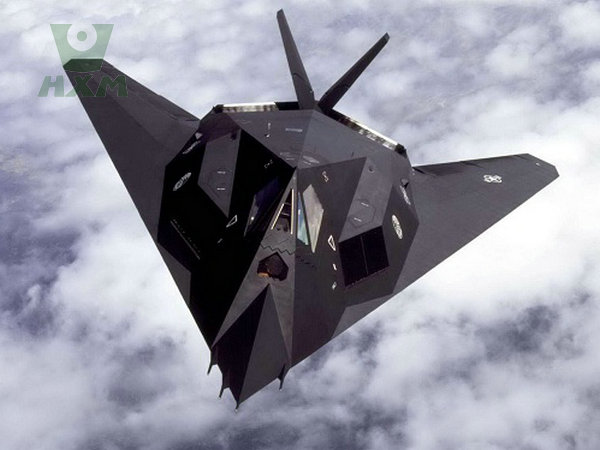
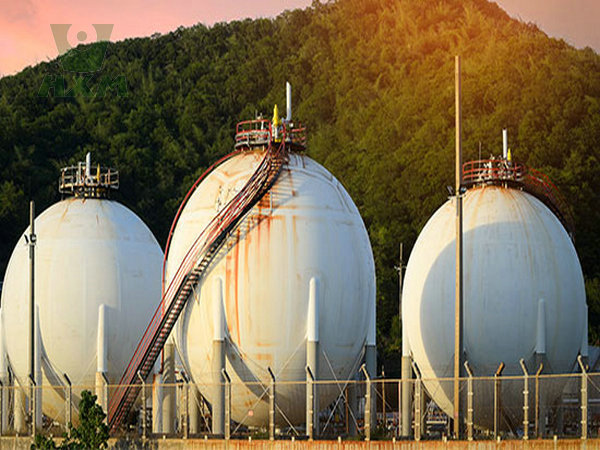
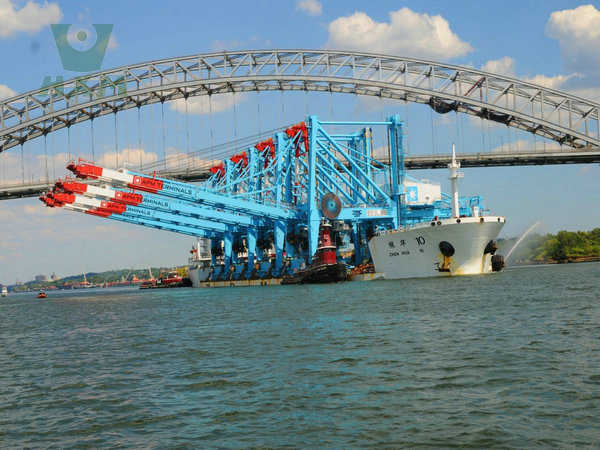
Considerations for Optimal Performance
To ensure optimal performance of Hastelloy alloys in various applications, several considerations must be taken into account:
Material Selection: Choosing the right alloy grade is crucial based on the specific corrosive environment and temperature conditions.
Fabrication Techniques: Proper welding, machining, and heat treatment practices are essential to maintain the corrosion resistance and mechanical properties of the alloys.
Inspection and Testing: Regular inspection and testing of Hastelloy components are necessary to detect any signs of corrosion or degradation and to ensure safe and reliable operation.
Environmental Factors: The presence of contaminants, such as chloride ions or oxygen, can affect the corrosion resistance of Hastelloy alloys. Therefore, it is important to control these factors in the operating environment.
Aspect | Details | Challenges |
---|---|---|
Welding | – Common methods: TIG (Tungsten Inert Gas), MIG (Metal Inert Gas), SAW (Submerged Arc Welding). – Use matching filler metals. – Post-weld heat treatment may be required for stress relief. | – Susceptibility to hot cracking. – Contamination from carbon or sulfur must be avoided. |
Machining | – Use slow speeds and high feed rates. – Carbide or ceramic cutting tools are recommended. – Coolants are essential to reduce heat buildup. | – High work hardening tendency. – Tool wear due to the alloy’s toughness. |
Forming | – Cold forming is preferred for thin sections. – Hot forming at 1600–2200°F (870–1200°C) for thicker sections. – Annealing may be required after forming. | – High strength and hardness make forming difficult. – Risk of cracking during bending. |
Heat Treatment | – Solution annealing at 1900–2100°F (1040–1150°C) followed by rapid cooling. – Stress relieving at lower temperatures (1100–1300°F or 600–700°C). | – Overheating can lead to grain growth and reduced corrosion resistance. |
Cutting | – Plasma cutting, laser cutting, or waterjet cutting are preferred. – Mechanical cutting requires high-power equipment. | – High toughness and hardness make cutting challenging. |
In Conclusion
The fabrication of Hastelloy corrosion resistant alloys involves a combination of material composition, key properties, manufacturing processes, and applications. By understanding these aspects, engineers and manufacturers can select the appropriate alloy grade and fabrication process to meet the specific requirements of their applications.
In summary, the fabrication of Hastelloy corrosion resistant alloys involves a combination of alloy grades, advanced manufacturing techniques, and careful consideration of material selection, fabrication techniques, inspection, and environmental factors. By understanding these aspects, engineers and manufacturers can optimize the performance of Hastelloy alloys in various applications, ensuring safe and reliable operation in harsh environments.