Alloy precision machining is a specialized manufacturing process that involves shaping and finishing alloy materials to exact specifications using advanced machining techniques. This process is critical for producing high-quality components used in industries such as aerospace, automotive, medical, and energy. Below is a detailed description of alloy precision machining, covering its key aspects, techniques, advantages, and applications.
Definition of Alloy Precision Machining
Alloy precision machining refers to the process of removing material from alloy workpieces to create parts with precise dimensions, tight tolerances, and high surface quality. This process is typically performed using computer-controlled machines such as CNC cuting (Computer Numerical Control) cuting mills, lathes, and grinders. Our company has the wholeheartly service for every customers, if you have any questions, our experts will offer the best solution for you.
Key Aspects of Alloy Precision Machining
Aspect | Description |
---|---|
Material Selection | Alloys such as Inconel, Titanium, Stainless Steel, and Aluminum are commonly used. |
Tolerances | Extremely tight tolerances, often within microns, are achieved. |
Surface Finish | High-quality surface finishes are achieved, reducing the need for additional post-processing. |
Complex Geometries | Complex shapes and intricate designs can be machined with high accuracy. |
Repeatability | CNC machines ensure consistent quality and repeatability across multiple parts. |
What is Alloy Precision Machining?
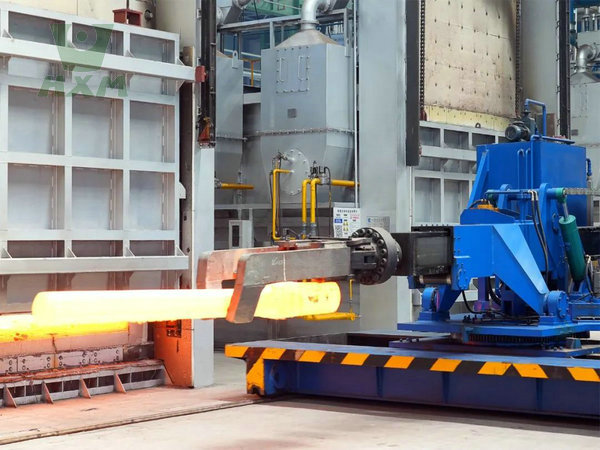
Alloy Precision Machining refers to the process of accurately manufacturing components and parts from alloy materials through a series of specialized techniques and equipment. In alloy precision machining, various processes are employed to achieve the desired shape, size, and surface finish of the components. These processes include, but are not limited to, milling, turning, drilling, grinding, and cutting. High-precision machinery and tools, such as CNC cuting (Computer Numerical Control) machines, are utilized to ensure that the finished components meet tight tolerances and specifications. Huaxiao Metal Supplier has the precision alloy and the quality is good, which alloy products have the assurance.
What are the steps involved in the precision machining process?
Alloy Precision machining is a highly controlled manufacturing process used to create parts with exact dimensions, tight tolerances, and high surface quality. It is widely used in industries such as aerospace, automotive, medical, and energy. Below is a detailed description of the steps involved in the precision machining process, presented in a structured format with tables for clarity. Huaxiao Metal Manufacturer has the all kinds of precision alloy, welcome to ask for price.
1. Design and Planning
Before machining begins, thorough design and planning are essential to ensure the final product meets specifications.
Step | Description |
---|---|
CAD Design | Create a detailed 3D model of the part using Computer-Aided Design (CAD) software. |
Material Selection | Choose the appropriate alloy (e.g., Inconel, Titanium, Stainless Steel) based on the application. |
Tolerance Analysis | Define the required tolerances and surface finishes for the part. |
Tooling Selection | Select the right cutting tools, fixtures, and machining equipment. |
CNC Programming | Develop a CNC program using CAM (Computer-Aided Manufacturing) software to guide the machine. |
Material Selection: The first step is to choose the appropriate material for the part based on its intended use, mechanical properties, and cost considerations. Alloy materials, such as aluminum, stainless steel, titanium, and nickel-based alloys, are commonly used in precision machining due to their combination of strength, corrosion resistance, and other favorable properties.
Design and Planning: Next, the part is designed using CAD (Computer-Aided Design) software. This step involves creating a detailed 3D model of the part, which is then used to generate a machining plan. The alloy precision machining plan outlines the specific operations, tooling, and setup requirements needed to machine the part to the desired specifications.
2. Workpiece Preparation
Proper preparation of the workpiece ensures accuracy and efficiency during machining.
Step | Description |
---|---|
Material Cutting | Cut the raw material into a size slightly larger than the final part dimensions. |
Workpiece Fixturing | Secure the workpiece firmly in the machining center using clamps, vices, or custom fixtures. |
Surface Cleaning | Clean the workpiece to remove dirt, oil, or debris that could affect machining accuracy. |
Setup and Tooling: Once the design is complete, the next step is to set up the alloy precision machining equipment and select the appropriate tooling. This includes installing the material in the machine, selecting the correct cutting tools, and configuring the machine settings based on the machining plan.
Machining Operations: The core of the alloy precision machining process involves performing the actual machining operations. These operations may include milling, turning, drilling, grinding, and other processes, depending on the specific requirements of the part. CNC (Computer Numerical Control) machines are commonly used to automate and control these operations with high precision.
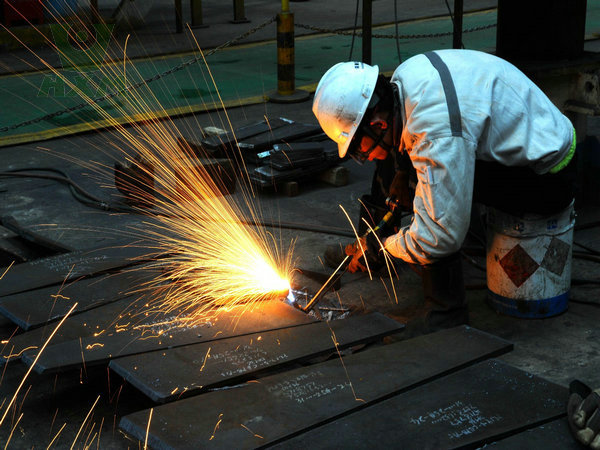
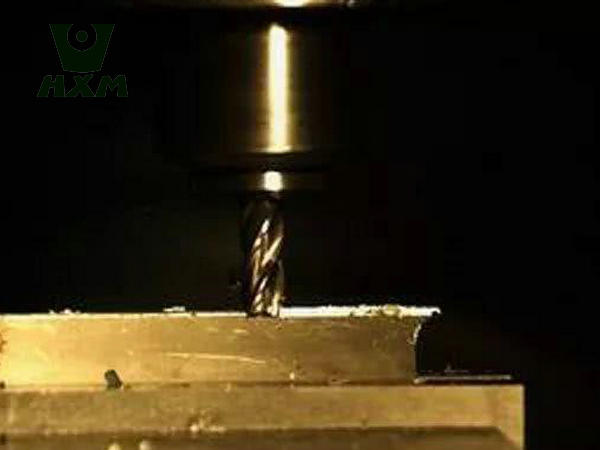
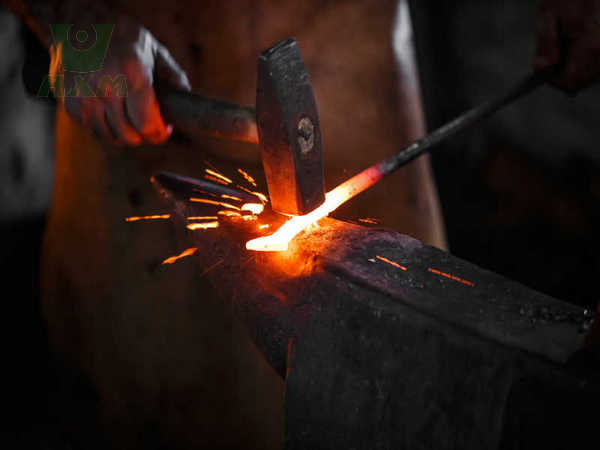
3. Machining Operations
The actual alloy precision machining process involves removing material from the workpiece to achieve the desired shape and dimensions.
Step | Description |
---|---|
Rough Machining | Remove large amounts of material quickly to get close to the final shape. |
Semi-Finishing | Refine the part geometry and prepare for final machining. |
Finishing | Achieve the final dimensions, tolerances, and surface finish using precise cutting tools. |
Drilling and Tapping | Create holes and threads as specified in the design. |
Inspection | Use measuring tools (e.g., micrometers, CMMs) to check dimensions during machining. |
In-Process Inspection: During the alloy machining process, regular inspections are conducted to ensure that the part is being machined to the specified dimensions and tolerances. This may involve measuring the part dimensions, checking the surface finish, and verifying the alignment and positioning of features.
Post-Machining Operations: After the primary machining operations are complete, additional post-machining operations may be required. These may include deburring, cleaning, and applying protective coatings or finishes to the part.
4. Post-Machining Processes
After machining, additional steps may be required to enhance the part’s properties or appearance.
Step | Description |
---|---|
Deburring | Remove sharp edges or burrs left from machining. |
Heat Treatment | Apply heat treatment (e.g., annealing, tempering) to improve mechanical properties. |
Surface Finishing | Apply coatings, polishing, or plating to improve surface quality and corrosion resistance. |
Cleaning | Clean the part to remove machining residues, oils, or contaminants. |
5. Quality Control and Inspection
Ensuring the part meets all specifications is a critical step in alloy precision machining.
Step | Description |
---|---|
Dimensional Inspection | Use tools like calipers, micrometers, and Coordinate Measuring Machines (CMMs) to verify dimensions. |
Surface Finish Check | Measure surface roughness using profilometers or surface testers. |
Functional Testing | Test the part’s functionality (e.g., fit, assembly, performance) if required. |
Documentation | Record inspection results and ensure compliance with design specifications. |
- Final Inspection and Quality Control: The final step in the alloy precision machining process is to conduct a thorough inspection and quality control check of the machined part. This involves measuring all critical dimensions, checking for defects or imperfections, and verifying that the part meets the specified requirements. If any issues are found, the part may need to be reworked or discarded.
Packaging and Shipment: Once the part has passed the final inspection, it is packaged and prepared for shipment to the customer. This may involve protecting the part from damage during transit and providing any necessary documentation or certifications.
6. Packaging and Delivery
The final step involves preparing the part for delivery to the customer.
Step | Description |
---|---|
Packaging | Protect the part from damage during transportation using appropriate packaging materials. |
Labeling | Label the package with part numbers, batch details, and handling instructions. |
Shipping | Deliver the part to the customer, ensuring timely and safe transportation. |
What are the methods equipment used in precision machining?
Methods
Precision Cutting
- It relies on high-precision, rigid machine tools and finely honed cutting tools to remove an extremely thin layer of metal from the workpiece surface at a very high or extremely low cutting speed, with a very small cutting depth and feed rate.
- It can significantly improve the machining accuracy of parts.
- It includes processes such as precision turning, and wide-blade precision planing.
High-gloss High-precision Grinding
- It also requires high precision and rigidity of the machine tool.
- The grinding process uses a finely dressed grinding wheel to produce multiple equal-height micro-cutting edges on each abrasive grain. With a very small grinding depth and under appropriate grinding pressure, very fine chips are cut from the workpiece surface, combined with the sliding, squeezing, and smoothing effects of the micro-cutting edges in a dull state, as well as the friction polishing effect of multiple no-feed grinding stages, to obtain very high machining accuracy and good physical and mechanical properties of the high-gloss surface.
- It includes precision grinding, ultra-precision grinding, and mirror grinding.
Equipment
CNC Milling Machines
- They use specialized rotating cutters to remove excess material from the workpiece.
- The direction, angle, pressure, and cutting tool speed can be varied to create different cutting effects.
- There are many variants of CNC milling machines, such as bed-type, box-type, C-type, floor-type, monolithic, gantry-type, horizontal drill-milling machines, knee-type, planer-type, turret-type, and double-column milling machines.
CNC Lathes
- In CNC turning, the workpiece rotates along a central axis, while a linearly moving cutting tool removes material from the workpiece.
- The cutting tool is usually non-rotating, unlike CNC milling machines.
- Single-point cutting tools are commonly used in this process.
CNC Drilling Machines
- In CNC drilling, the workpiece remains stationary, while a rotating drill bit moves around the workpiece and drills holes in it.
- These holes may be used for part assembly or for aesthetic purposes.
- By changing the size of the drill bit, the CNC drilling machine can create holes of different sizes. By controlling the machine tool calibration, the depth of the holes can be adjusted.
Multi-axis CNC Machining Centers
- They are an integrated machining system capable of performing complex machining tasks.
- Other alternative names for this process include electric discharge machining (EDM), die-casting, wire erosion, wire burning, or spark erosion.
- EDM is only applicable to metals because they conduct electricity.
Huaxiao Metal Supplier has the precision alloy, and other alloy products also have, such as the hastelloy, incoloy, inconel, monel, and titanium alloyand so on.
Differences between precision machining and traditional machining
Alloy Precision machining and traditional alloy precision machining each have their own unique advantages and are suitable for different types of manufacturing applications. As the exporter, our company has the good quality of alloy in China. Alloy Precision Machining has two ways of precision machining and traditional machining.
Precision Machining
Alloy Precision machining is a type of manufacturing process that involves the use of advanced techniques and equipment to achieve extremely high levels of accuracy and surface finish on machined parts. It typically employs specialized machine tools and cutting tools that are capable of operating with minute precision.
The key characteristics of precision machining include:
- High Accuracy: Alloy Precision machining can achieve tolerances and dimensional accuracy that are significantly tighter than traditional machining methods.
- High Surface Finish: The surfaces of parts produced through alloy precision machining often have a very smooth and polished appearance, which is critical for applications where friction, wear, and corrosion are concerns.
- Use of Advanced Materials: Alloy Precision machining is often used to process advanced materials such as aerospace alloys, titanium, and ceramics, which require specialized equipment and techniques to machine effectively. This is important for applications where the surface properties of the part are critical. Alloy precision machining is a good way to improve the alloy precision.
Traditional Machining
Traditional machining, on the other hand, refers to a broad range of manufacturing processes that have been used for centuries to shape and form materials into desired shapes and sizes. It typically involves the use of tools such as lathes, milling machines, drills, and grinders to remove excess material from a workpiece.
The main characteristics of traditional machining include:
- Versatility: Traditional alloy precision machining methods can be used to produce a wide range of parts and components, from simple brackets and fasteners to complex assemblies and machinery.
- Cost-effectiveness: For many applications, traditional alloy precision machining is a cost-effective way to produce parts in large quantities.
- Operator Skill: The success of traditional alloy precision machining often depends on the skill and experience of the operator, who must control the machine tools and ensure that the correct cutting parameters are used.
- Accuracy and Precision: Alloy Precision machining offers significantly higher levels of accuracy and precision than traditional machining. This is due to the use of advanced machine tools, cutting tools, and measurement equipment.
Advantages and disadvantages of precision machining
Precision machining offers numerous advantages, including high accuracy, versatility in material and design, and cost-effectiveness in large-scale production. However, it also has its disadvantages, such as high initial investment, time-consuming processes, material waste, and limitations in material compatibility.
When comparing precision machining to other manufacturing processes, it is essential to consider the specific requirements of the project, such as the required accuracy, material type, production volume, and budget. Precision machining may be the optimal choice for projects requiring high precision and intricate designs, but it may not be the most cost-effective or time-efficient option for all types of production. Therefore, a thorough evaluation of the project requirements and constraints is necessary to determine the most suitable manufacturing process.
Advantages of Precision Machining
Precision machining offers numerous benefits that make it indispensable in various industries. Firstly, it ensures high accuracy and precision in the final product. This is critical in fields such as aerospace, medical devices, and automotive components where even the slightest deviation can compromise performance and safety.
Secondly, precision machining allows for intricate designs and complex geometries to be created. Advanced machining techniques, such as computer numerical control (CNC) milling and turning, enable the production of parts with intricate details and tight tolerances.
Moreover, precision machining is a versatile process that can be applied to a wide range of materials, including metals, plastics, and composites. This versatility makes it a flexible manufacturing option for a diverse array of applications.
Additionally, precision machining is often more cost-effective in the long run, especially when producing large quantities of parts. With automated and semi-automated processes, labor costs are minimized, and production efficiency is maximized.
Disadvantages of Precision Machining
Despite its many advantages, precision machining also has its limitations. One significant drawback is the high initial investment required for specialized equipment and machinery. High-precision machines, such as CNC lathes and milling machines, can be very expensive to purchase and maintain.
Furthermore, precision machining can be a time-consuming process, especially when producing small batches or custom parts. The setup and programming of machines, as well as the meticulous inspection of finished parts, can add to the overall production time.
Another consideration is the potential for material waste. While precision machining can minimize waste compared to other manufacturing processes, there is still a significant amount of scrap material generated, especially when producing complex geometries.
Lastly, precision machining may not be the most suitable process for all types of materials. Some materials, such as brittle ceramics or soft plastics, may not be easily machined to high precision without causing damage or deformation.
Balancing precision machining with traditional machining
Balancing alloy precision machining with traditional machining involves recognizing the strengths and limitations of both processes and determining the most appropriate combination for a given manufacturing task. Here’s an analysis of how to achieve this balance:
Strengths of Precision Machining
Alloy Precision machining, particularly when leveraging advanced technologies like computer numerical control (CNC), offers unparalleled accuracy and repeatability. It is ideal for producing complex geometries and tight tolerances, which are critical in industries such as aerospace, medical, and automotive. CNC machines can operate continuously with minimal human intervention, leading to increased productivity and reduced labor costs in large-scale production.
Strengths of Traditional Machining
Traditional machining, often manual or semi-automatic, has its own set of advantages. It typically requires less initial investment in equipment compared to precision machining. Additionally, traditional machining can be more adaptable to small-batch production or prototype development, where the flexibility to quickly adjust processes is beneficial. Operators with extensive experience can often achieve good results even with simpler machinery, making it a viable option for shops with limited resources.
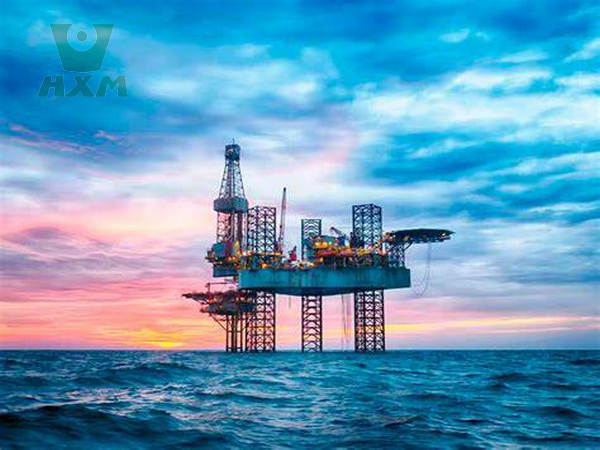
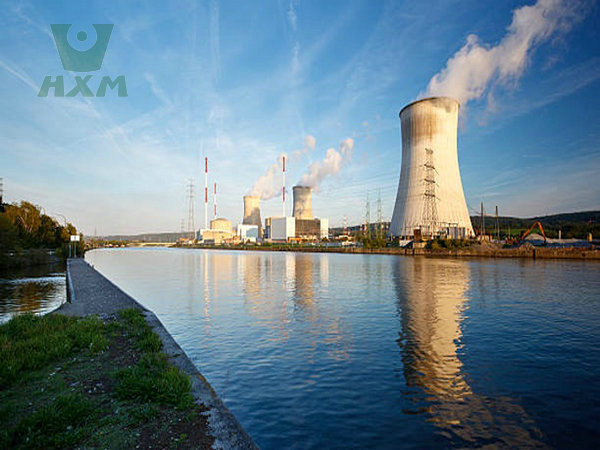
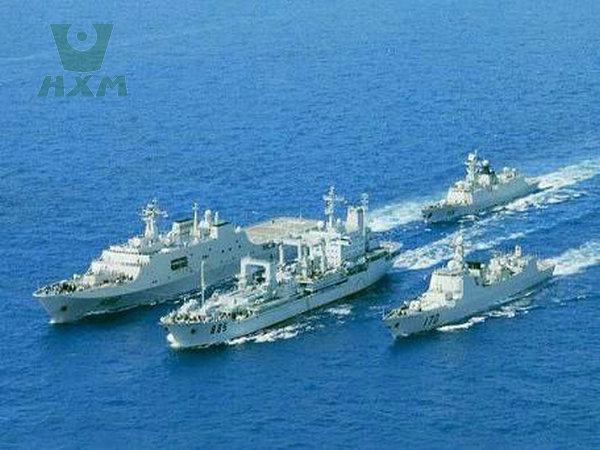
Balancing the Two
To balance alloy precision machining with traditional machining, manufacturers should consider the following factors:
Project Requirements: Evaluate the specific accuracy, material, and design requirements of the project. If high precision and intricate geometries are necessary, precision machining may be the best choice. For simpler designs or larger batches where cost is a primary concern, traditional machining might be more suitable.
Production Volume: Consider the production volume. Precision machining is often more cost-effective in high-volume production due to its automation and efficiency. For low-volume or prototype production, traditional machining may offer a more flexible and cost-effective solution.
Material Considerations: The type of material being machined can also influence the choice of process. Some materials may be more difficult to machine to high precision due to their hardness or brittleness, necessitating traditional methods. Conversely, precision machining can offer better surface finish and dimensional accuracy for certain materials.
Skill and Experience: The skill and experience of the operators should also be taken into account. Highly skilled operators can often achieve good results with traditional machinery, while precision machining may require specialized training and programming skills.
Cost Analysis: Conduct a thorough cost analysis to compare the initial investment, operational costs, and potential waste associated with each process. This will help in making an informed decision that aligns with the project’s budget and profitability goals.
Balancing alloy precision machining with traditional machining requires a nuanced understanding of the strengths and limitations of each process, as well as a detailed analysis of the project’s specific requirements. By considering factors such as project requirements, production volume, material considerations, skill and experience, and cost analysis, manufacturers can make informed decisions that optimize efficiency, accuracy, and cost-effectiveness. Ultimately, the goal is to select the most appropriate combination of processes to meet the project’s objectives while maximizing overall value. Alloy precision machining is a techique in processing alloy for a solution in order to more concrete.
Requirements for machining technicians
Machining technicians play a crucial role in the manufacturing industry, responsible for operating, maintaining, and troubleshooting various machining equipment to produce precision parts and components. To excel in this position, machining technicians must meet a series of rigorous requirements that encompass both technical skills and personal attributes. Below is an English introduction to the requirements for machining technicians:
Technical Skills and Knowledge
- Machining Fundamentals:
- A solid understanding of basic machining principles, including cutting tools, workpiece materials, and machining processes.
- Familiarity with various machining operations such as milling, turning, drilling, grinding, and others.
- Machine Operation:
- Proficiency in operating a range of machine tools, including CNC (Computer Numerical Control) lathes, milling machines, grinders, and drilling machines.
- Ability to read and interpret blueprints, technical drawings, and machine specifications.
- Programming Skills:
- Knowledge of G-code and M-code programming for CNC machines.
- Experience with CAM (Computer-Aided Manufacturing) software for generating machining programs.
- Metrology and Inspection:
- Skill in using precision measurement tools such as micrometers, calipers, and gauges.
- Understanding of inspection techniques and quality control standards.
- Maintenance and Troubleshooting:
- Ability to perform routine maintenance on machine tools, including lubrication, cleaning, and alignment.
- Proficiency in diagnosing and troubleshooting machine malfunctions.
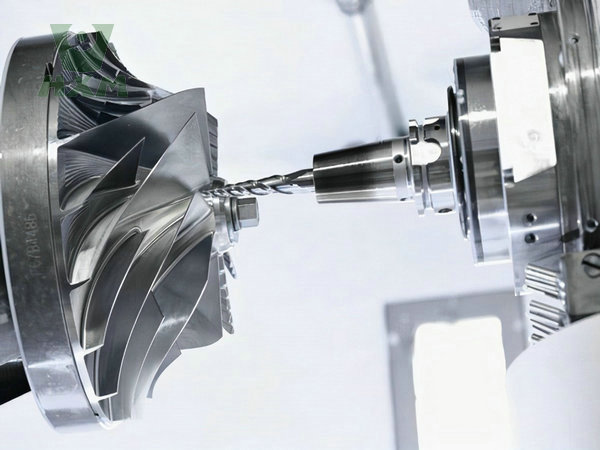
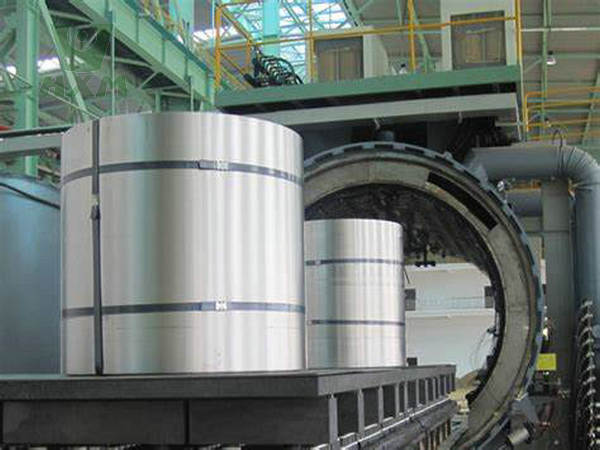
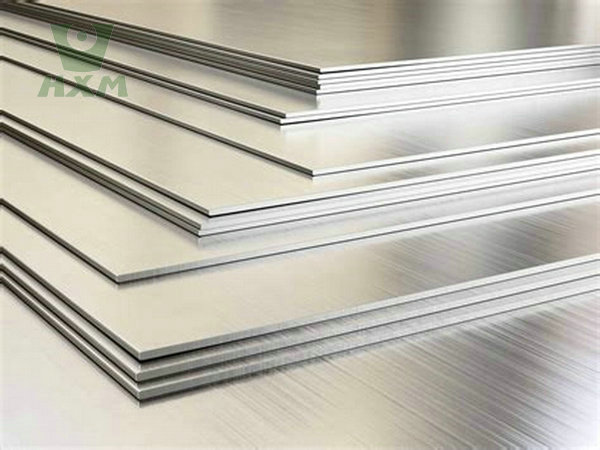
Personal Attributes and Soft Skills
- Attention to Detail:
- A meticulous approach to work, ensuring precision and accuracy in all machining operations.
- Problem-Solving Skills:
- Analytical thinking and the ability to identify and resolve complex technical issues.
- Adaptability:
- Flexibility to adapt to new technologies, processes, and materials as the manufacturing industry evolves.
- Teamwork:
- Strong communication skills and the ability to work effectively within a team environment.
- Collaboration with engineers, designers, and other technicians to achieve manufacturing goals.
- Safety Awareness:
- A commitment to adhering to safety protocols and procedures to prevent accidents and injuries.
- Familiarity with OSHA (Occupational Safety and Health Administration) regulations and industry safety standards.
- Continuous Learning:
- A willingness to stay updated with the latest advancements in machining technology and practices.
- Participation in training programs and professional development opportunities to enhance skills and knowledge.
Educational Background and Certifications
- Education:
- Typically, a high school diploma or equivalent is required, with relevant coursework in mathematics, physics, and engineering.
- Vocational training or an associate degree in machining technology can provide a strong foundation for a career in this field.
- Certifications:
- Pursuing certifications from industry-recognized organizations, such as the National Institute for Metalworking Skills (NIMS) or the American Society of Mechanical Engineers (ASME), can demonstrate a technician’s expertise and commitment to excellence.
Typical costs of precision machining
The typical costs of precision machining encompass various factors, each of which can significantly influence the overall expenditure. Below is an analysis of these costs:
1. Machining Cost
- Labor and Overhead: This includes the cost of labor required to operate the machine tools and the overhead expenses associated with running the machining operation. The labor cost may vary depending on the complexity of the job and the skill level of the technicians. Overhead costs include rent, utilities, and other administrative expenses.
- Cycle Time: The time required to complete a machining operation, also known as cycle time, directly affects the machining cost. A shorter cycle time typically results in lower labor and overhead costs per piece.
2. Material Cost
- Raw Material: The cost of the raw material used in the precision machining process. This can vary widely depending on the type of material (e.g., metal, plastic, ceramic) and its grade or quality.
- Material Waste: Precision machining often involves removing excess material to achieve the desired shape and size. The cost of material waste should be considered, as it represents material that is not utilized in the final product.
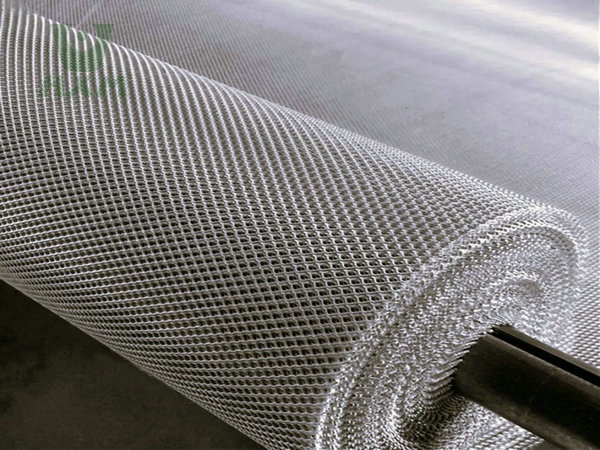
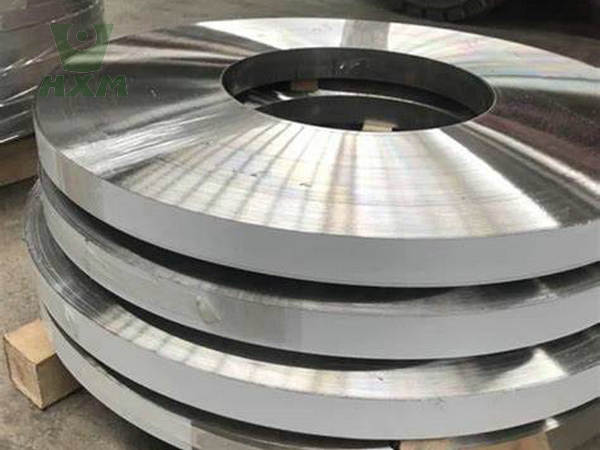
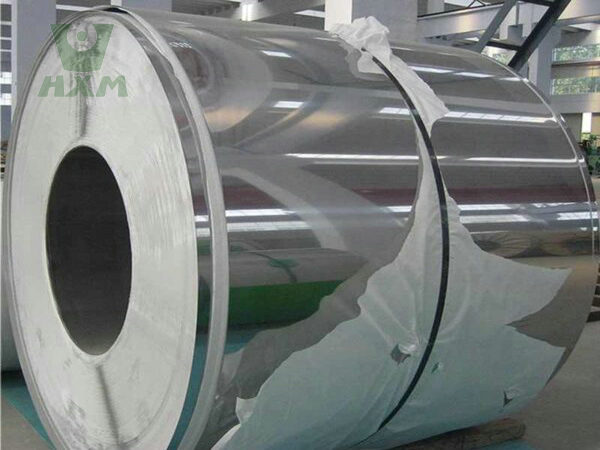
3. Tool Cost
- Tool Purchase and Maintenance: The cost of purchasing and maintaining the cutting tools used in precision machining. High-quality tools are essential for achieving precision and accuracy, but they also come with a higher price tag.
- Tool Life: The life of a cutting tool is finite and depends on various factors such as material hardness, cutting speed, and feed rate. As tool life decreases, the frequency of tool replacement increases, thereby increasing the tool cost.
4. Cost of Non-productive Time (Set-up Costs)
- Machine Set-up: The time and cost associated with setting up the machine tools for a specific machining operation. This includes aligning the machine, installing tools, and setting up the workpiece.
- Changeovers: When switching from one job to another, additional set-up time and costs may be incurred due to the need to reconfigure the machine tools and tools.
5. Additional Factors
- Machine Depreciation: The cost of depreciating the machine tools over their useful life. This is a fixed cost that should be considered when evaluating the overall cost of precision machining.
- Quality Control and Inspection: The cost of performing quality control and inspection activities to ensure that the machined parts meet the specified tolerances and requirements.
- Post-processing Costs: Costs associated with post-processing activities such as cleaning, coating, and packaging of the machined parts.
Analysis
- Variable Costs vs. Fixed Costs: Machining cost and tool cost are variable costs that increase with production volume, while material cost and the cost of non-productive time (set-up costs) can be considered fixed costs per job or batch.
- Optimization Opportunities: To minimize costs, manufacturing companies may seek to optimize the machining process by reducing cycle time, improving tool life, and minimizing material waste.
- Cost-benefit Analysis: When evaluating different machining options, a cost-benefit analysis should be performed to weigh the trade-offs between cost and performance.
In conclusion, the typical costs of alloy precision machining are multifaceted and include machining cost, material cost, tool cost, and the cost of non-productive time. By understanding these costs and their underlying factors, manufacturing companies can make informed decisions to optimize their machining processes and minimize overall expenditure.
Techniques Used in Alloy Precision Machining
Alloy Precision Machining techniques used in alloy precision machining are diverse and tailored to the specific requirements of the application. By combining these techniques with advanced machine tools and computer-aided manufacturing (CAM) software, manufacturing companies can produce high-quality, precision-machined alloy components that meet the most demanding specifications. Welcome to ask for the lastest price and inquiry.
Technique | Description |
---|---|
CNC Milling | Uses rotating cutting tools to remove material from the workpiece. |
CNC Turning | Rotates the workpiece while a cutting tool removes material to create cylindrical parts. |
Grinding | Uses abrasive wheels to achieve fine finishes and tight tolerances. |
EDM (Electrical Discharge Machining) | Uses electrical discharges to remove material, ideal for hard alloys and complex shapes. |
Laser Cutting | Uses a high-power laser to cut and shape alloy materials with high precision. |
Waterjet Cutting | Uses a high-pressure stream of water mixed with abrasive particles to cut alloys. |
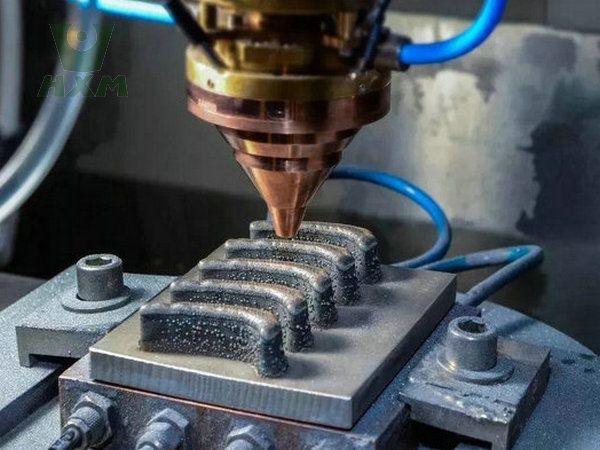
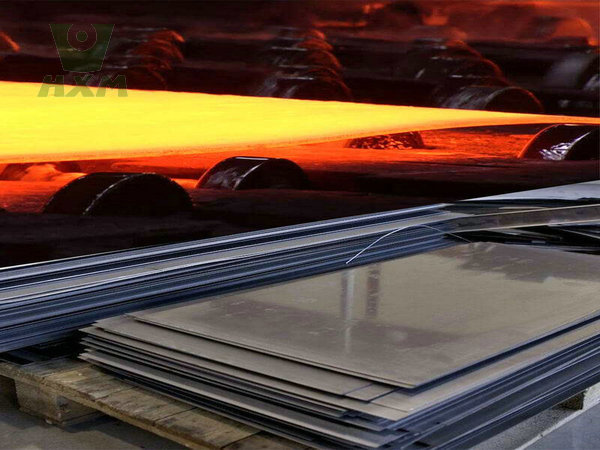
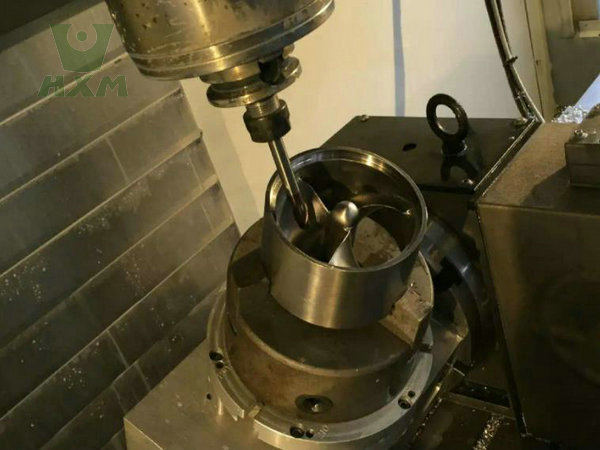
Applications of Alloy Precision Machining
Precision Alloy
Alloy precision machining plays a pivotal role across various industries, offering unparalleled accuracy and reliability in component manufacturing. It is extensively utilized in the aerospace sector for producing high-performance engine parts and structural components, ensuring airworthiness and efficiency. In the automotive industry, alloy precision machining enhances the durability and performance of critical parts such as gearboxes and engine blocks. Medical device manufacturers rely on this technology to create precision instruments and implants with strict tolerances and surface finishes. Additionally, electronics and semiconductor industries benefit from alloy precision machining for the fabrication of intricate components and assemblies. Overall, the versatility and precision of alloy machining techniques make them indispensable in advanced manufacturing. Huaxiao Metal Supplier is professional and creditable in China.
Industry | Applications | Examples |
---|---|---|
Aerospace | Turbine blades, engine components. | Machining Inconel 718 for jet engine parts. |
Automotive | Engine components, transmission parts. | Precision machining of aluminum alloy pistons. |
Medical | Surgical instruments, implants. | Machining Titanium alloy for orthopedic implants. |
Energy | Turbine components, heat exchangers. | Precision machining of Stainless Steel for nuclear reactor parts. |
Electronics | Heat sinks, connectors. | Machining copper alloys for electronic components. |
How to Reduce the Cost of Precision Machining: Strategies and Ways
Reducing the cost of alloy precision machining involves several strategic approaches. Firstly, selecting the right alloy material that balances machinability, durability, and cost is crucial. Materials like aluminum and certain grades of steel can offer cost savings due to their ease of machining.
Optimizing material utilization by using advanced CAD software to nest parts efficiently reduces waste and improves yield. Additionally, specifying realistic tolerances based on functional requirements helps avoid unnecessary precision that drives up costs.
Implementing efficient machining techniques such as high-speed machining (HSM) and multi-axis machining can drastically cut cycle times and reduce tool wear, thereby lowering labor and tool costs.
Automation and digitalization through CAM software and automated quality control systems enhance precision and efficiency, minimizing rework and scrap.
Finally, strategic outsourcing to experienced suppliers and investing in workforce training for advanced machining techniques can further reduce costs while maintaining high standards of quality and productivity in alloy precision machining.
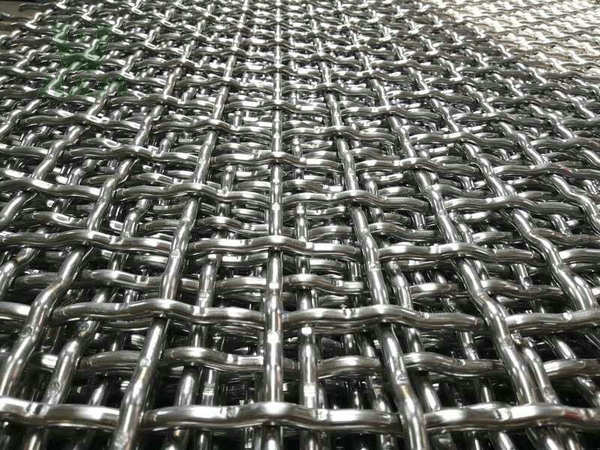
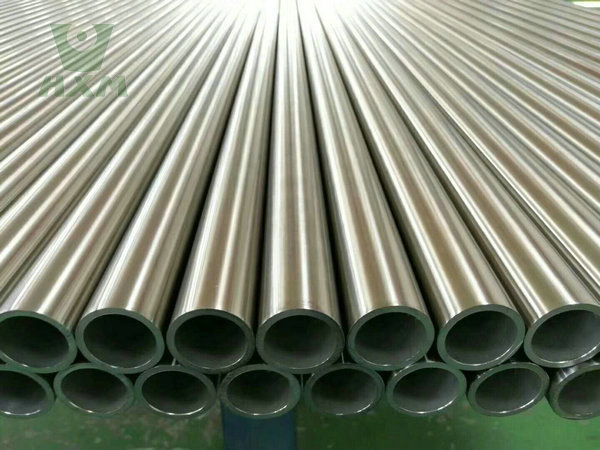
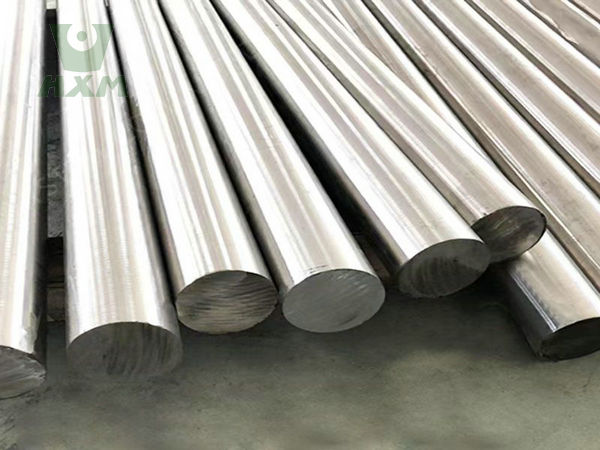
Challenges in Alloy Precision Machining
Alloy precision machining faces several challenges due to the unique properties of advanced materials like Inconel, Titanium, and Stainless Steel. These materials are often hard and tough, leading to rapid tool wear and increased machining costs. Heat generation during machining can affect both the workpiece and tools, requiring advanced cooling systems. Achieving tight tolerances and high surface finishes demands skilled operators and precise CNC programming. Additionally, the high cost of raw materials and specialized tooling adds to the overall expense. Despite these challenges, advancements in technology and techniques continue to improve efficiency and quality in alloy precision machining. Huaxiao Metal Manufacturer has the precision alloy and the customerized service for you.
Challenge | Description |
---|---|
Material Hardness | Some alloys, like Inconel and Titanium, are difficult to machine due to their hardness. |
Tool Wear | High wear rates of cutting tools when machining hard alloys. |
Heat Generation | Excessive heat can affect the material properties and tool life. |
Cost | High initial investment in CNC machines and tooling. |
Skill Requirement | Requires skilled operators and programmers. |
In Conclusion
Precision machining is a critical process for producing high-quality, complex components used in various industries. By following a structured approach—from design and planning to quality control and delivery—manufacturers can achieve tight tolerances, superior surface finishes, and consistent quality. This process enables the production of reliable and high-performance parts, making it indispensable in modern manufacturing.
Alloy precision machining is a critical process for producing high-quality, complex components used in various industries. By leveraging advanced machining techniques and CNC technology, manufacturers can achieve tight tolerances, superior surface finishes, and consistent quality. Despite the challenges, the advantages of alloy precision machining make it an indispensable part of modern manufacturing, enabling the production of reliable and high-performance parts.