Nickel 825 and Inconel 825 are widely recognized nickel-chromium-based superalloys known for their exceptional strength, corrosion resistance, and ability to perform in extreme environments. While they are essentially the same material, there are subtle differences in branding, quality control, and market perception.
Below is a comprehensive analysis of their similarities and differences across various aspects.
While they are essentially the same material, Inconel 825 is a trademarked name by Special Metals Corporation, whereas Nickel Alloy 825 is the generic term.
Nickel Alloy 825: A generic term for a nickel-chromium-molybdenum alloy with excellent corrosion resistance and high-temperature strength. It is produced by various manufacturers worldwide.
Inconel 825: A trademarked name by Special Metals Corporation for the same alloy. It is known for its stringent quality control and consistency.
Huaxiao Metal Supplier has the inconel products for sale. Our company has the customerized services for any clients and the alloy has assurrance. Of course, we also provide the specialized solutions for sloving every alloy problems.
Nickel Alloy 825 and Inconel 825
Inconel 825 Product Forms
Chemical Composition
Both alloys have identical chemical compositions, as shown below:
Element | Composition | Purpose/Effect |
---|---|---|
Nickel (Ni) | 38–46% | Provides the base matrix, offering high strength and corrosion resistance. |
Chromium (Cr) | 19.5–23.5% | Enhances oxidation and corrosion resistance, especially at high temperatures. |
Iron (Fe) | 22% min | Acts as a stabilizer and improves resistance to stress corrosion cracking (SCC). |
Molybdenum (Mo) | 2.5–3.5% | Improves resistance to pitting and crevice corrosion. |
Copper (Cu) | 1.5–3.0% | Enhances resistance to sulfuric and phosphoric acids. |
Titanium (Ti) | 0.6–1.2% | Stabilizes the alloy against sensitization during welding. |
Carbon (C) | 0.05% max | Kept low to minimize carbide formation and maintain weldability. |
Manganese (Mn) | 1.0% max | Acts as a deoxidizer and improves hot workability. |
Silicon (Si) | 0.5% max | Improves oxidation resistance and fluidity during casting. |
Sulfur (S) | 0.03% max | Kept low to avoid hot cracking during welding. |
Aluminum (Al) | 0.2% max | Works with titanium to stabilize the alloy. |
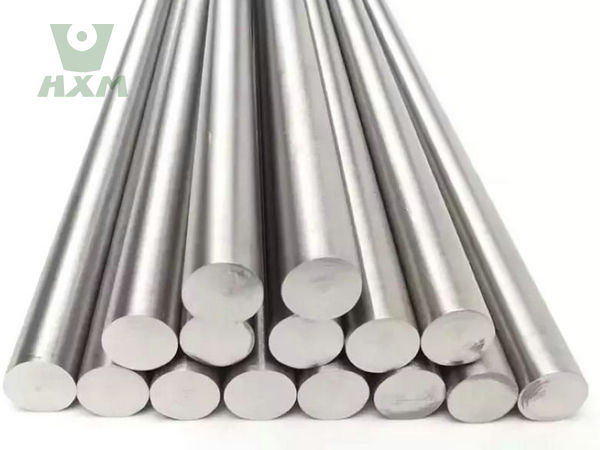
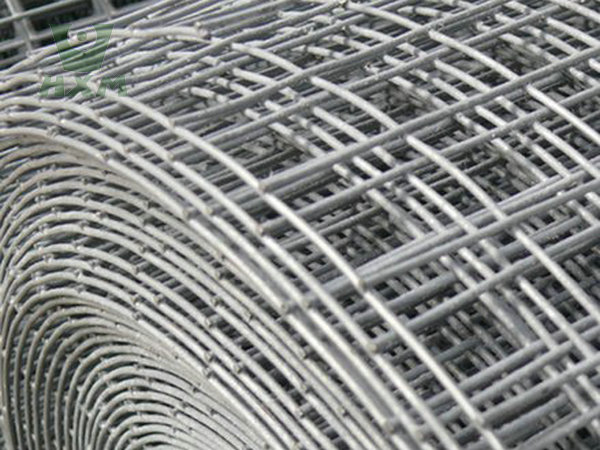
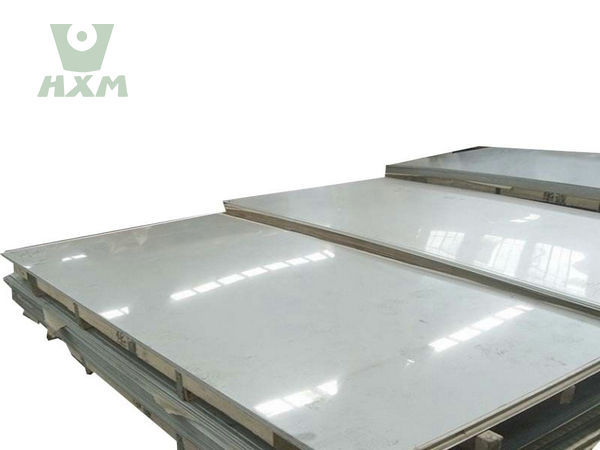
It’s important to note that the chemical composition may vary slightly depending on the specific manufacturer and application requirements. Therefore, it’s always advisable to refer to the material certificate provided by the supplier for accurate chemical composition details. Additionally, both Nickel Alloy 625 and Inconel 625 are known for their high-performance characteristics, including high strength, excellent corrosion resistance, and good weldability, making them suitable for various demanding applications such as marine, nuclear, and chemical processing industries.
Mechanical Properties
Both alloys exhibit the same mechanical properties due to their identical composition:
Property | Value |
---|---|
Tensile Strength | 586–758 MPa (85–110 ksi) |
Yield Strength | 241–586 MPa (35–85 ksi) |
Elongation | 30–50% |
Hardness (Rockwell B) | 80–120 HRB |
Density | 8.14 g/cm³ (0.294 lb/in³) |
Melting Point | 1370–1400°C (2500–2550°F) |
Corrosion Resistance
Both materials exhibit excellent corrosion resistance due to their high nickel and chromium content:
Oxidizing Environments: High chromium content provides resistance to oxidation and scaling at high temperatures.
Reducing Environments: Molybdenum and niobium enhance resistance to pitting and crevice corrosion.
Stress Corrosion Cracking (SCC): Both alloys are resistant to SCC in chloride and sulfide environments.
Inconel 825 Advantages and Limitations
Inconel 825 offers numerous advantages, including exceptional corrosion resistance, high-temperature strength, and versatility in fabrication. These properties make it a preferred choice for demanding applications in industries such as chemical processing, oil and gas, and marine engineering. However, its high cost, challenging machining requirements, and susceptibility to sensitization and hydrochloric acid corrosion are notable limitations. Understanding these advantages and limitations is crucial for selecting the right material for specific applications, ensuring optimal performance and cost-effectiveness.
Huaxiao Metal Manufacturer is professional and experienced in China, our company has over 10 years in alloy industry, which we are reliable and creditable, and our products are good quality in producing carefully to control quality. Service are personalized for every customer and providing the customerized solutions for the any problems. Welcome to ask for the lastest price about alloy products.
Advantage | Description |
---|---|
Excellent Corrosion Resistance | Resists corrosion in sulfuric and phosphoric acids, as well as in chloride and sulfide environments. |
High Temperature Strength | Maintains mechanical properties at elevated temperatures, making it suitable for high-temperature applications. |
Resistance to Stress Corrosion Cracking (SCC) | Performs well in environments prone to SCC, such as those containing chlorides and sulfides. |
Versatility in Fabrication | Can be welded, machined, and formed using standard techniques, making it adaptable to various applications. |
Oxidation Resistance | High chromium content provides excellent resistance to oxidation and scaling at high temperatures. |
Resistance to Pitting and Crevice Corrosion | Molybdenum and copper enhance resistance to localized corrosion in aggressive environments. |
Wide Range of Applications | Suitable for use in chemical processing, oil and gas, marine engineering, and pollution control. |
Stability in Reducing Environments | Performs well in reducing environments, such as those containing sulfuric and phosphoric acids. |
Limitation | Description |
---|---|
High Cost | More expensive than standard stainless steels and other nickel alloys, which can limit its use in budget-sensitive projects. |
Difficult Machining | High strength and work-hardening tendency make machining challenging, requiring specialized tools and techniques. |
Susceptibility to Sensitization | Prolonged exposure to high temperatures (425–815°C or 800–1500°F) can lead to sensitization, reducing corrosion resistance. |
Limited Resistance to Hydrochloric Acid | Not recommended for use in hydrochloric acid environments, where it may suffer from severe corrosion. |
Heavy Weight | Higher density compared to some other materials, which may be a disadvantage in weight-sensitive applications. |
Complex Heat Treatment | Requires precise heat treatment to maintain optimal properties, adding to the complexity and cost of fabrication. |
Limited Availability | While widely available, the trademarked Inconel 825 may have limited suppliers compared to generic Nickel Alloy 825. |
Aspect | Advantages | Limitations |
---|---|---|
Corrosion Resistance | Excellent in sulfuric, phosphoric, and chloride environments. | Susceptible to hydrochloric acid and sensitization at high temperatures. |
Mechanical Properties | High strength and stability at elevated temperatures. | Difficult to machine due to work-hardening tendency. |
Fabrication | Versatile and adaptable to welding, forming, and machining. | Requires precise heat treatment and specialized tools. |
Cost | Provides long-term value in corrosive environments. | High initial cost compared to stainless steels and other alloys. |
Applications | Suitable for a wide range of industries, including chemical processing and oil and gas. | Limited use in weight-sensitive applications due to higher density. |
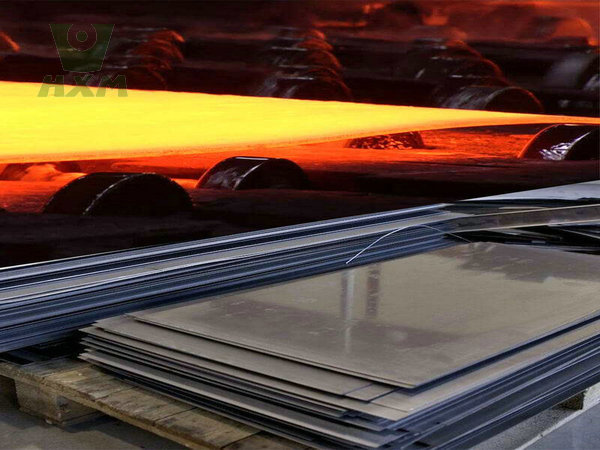
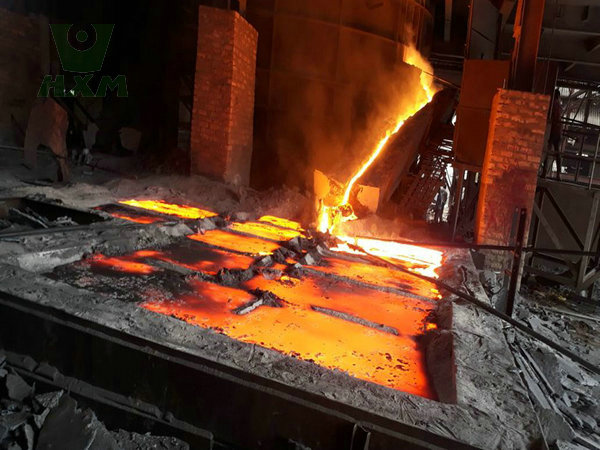
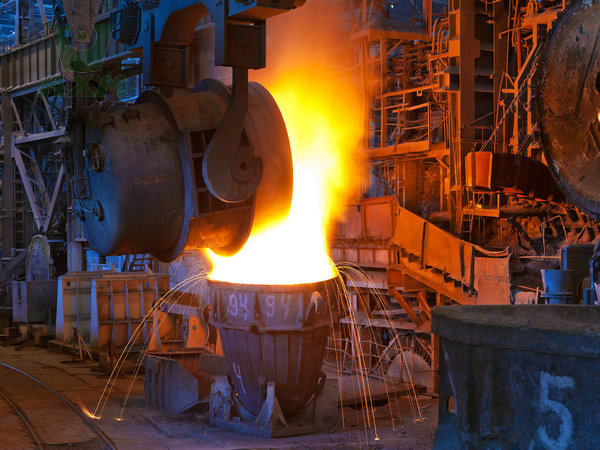
Fabrication Machining Characteristics
Below is a detailed comparison of their properties, applications, and fabrication characteristics.
- Welding: TIG, MIG, and plasma arc welding are commonly used. Post-weld heat treatment is often required to relieve stresses.
- Machining: Requires carbide or ceramic tools, slow speeds, and high feed rates. Coolants are essential to prevent overheating.
- Forming: Can be cold or hot formed, but hot forming is preferred for complex shapes.
- Heat Treatment: Solution annealing at 925–980°C (1700–1800°F) followed by rapid cooling is standard.
Similarities
Chemical Composition: Identical.
Mechanical Properties: Identical.
Corrosion Resistance: Identical.
Applications: Used interchangeably in the same industries.
Fabrication: Similar techniques and challenges.
Differences
Aspect | Nickel Alloy 825 | Inconel 825 |
---|---|---|
Branding | Generic term used by multiple manufacturers. | Trademarked name by Special Metals Corporation. |
Quality Control | May vary depending on the manufacturer. | Strict quality control under the Inconel brand. |
Market Perception | Often perceived as a cost-effective alternative. | Perceived as a premium product due to brand reputation. |
Availability | Widely available from various suppliers. | Primarily supplied by Special Metals and licensed distributors. |
Nickel Alloy 825 and Inconel 825 Applications
Both Nickel Alloy 825 and Inconel 825 are used in demanding applications, including:
Chemical Processing: Reactors, heat exchangers, and piping systems for sulfuric and phosphoric acid environments.
Oil and Gas: Downhole tools, valves, and wellhead components.
Pollution Control: Scrubbers, waste treatment systems, and flue gas desulfurization equipment.
Marine Engineering: Seawater piping, propeller shafts, and offshore platforms.
Nuclear Industry: Fuel reprocessing and waste disposal systems.
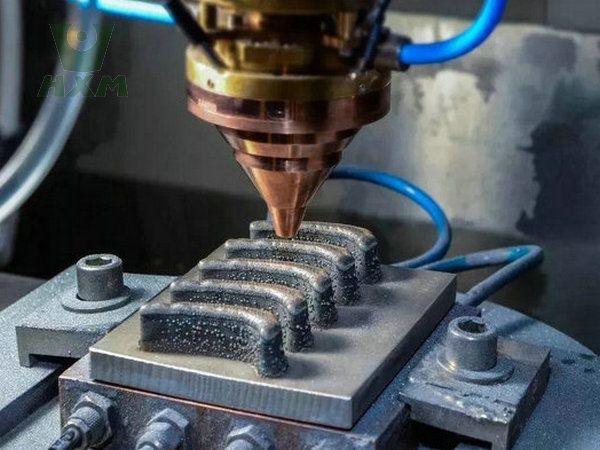
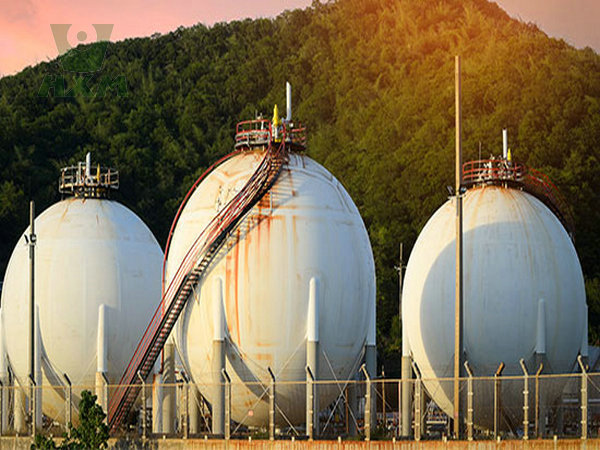
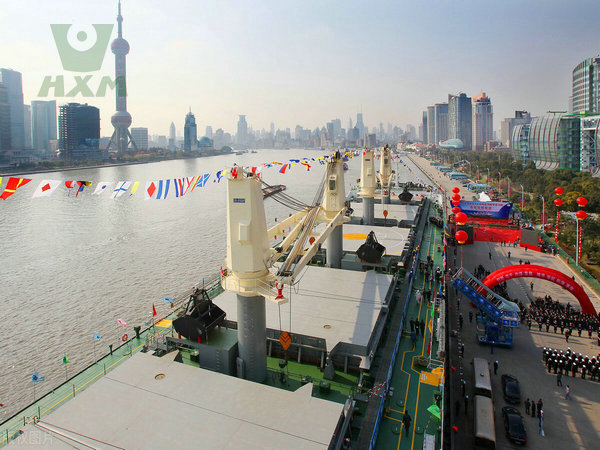
In Conclusion
Nickel Alloy 825 and Inconel 825 are functionally identical in terms of chemical composition, mechanical properties, and performance. The primary differences lie in branding, quality control, and market perception. While Nickel Alloy 825 is a generic term used by multiple manufacturers, Inconel 825 is a trademarked product known for its stringent quality standards. Both alloys are highly valued for their strength, corrosion resistance, and versatility in extreme environments, making them indispensable in industries such as chemical processing, oil and gas, and marine engineering.
Huaxiao Metal Supplier has the complete system for customers to services for sale, which our company is professional alloy top of manufacturer in China. If you have any questions , welcome to inquiry to our company. We have the professional team for you offer the complete solutions, I am convienced that your questions will be well sloved by our experts, which you can consult my staff customer service for any questions about alloys for free, and we will be happy to answer and provide you with various customized solutions for.