Nickel 600 and Inconel 600 are often used interchangeably, but they refer to the same material. Inconel Alloy 600 is a trademarked name by Special Metals Corporation, while Nickel Alloy 600 is the generic term for this nickel-chromium alloy. Below is a detailed comparison of their properties, applications, and fabrication characteristics.
Nickel 600 and Inconel 600 are the generic term used to describe this material. Both are widely recognized for their exceptional resistance to high temperatures, oxidation, and corrosion, making them indispensable in industries such as aerospace, chemical processing, nuclear engineering, and power generation. Huaxiao Metal Supplier has the inconel products for sale. Our company has the customerized services for any clients and the alloy has assurrance.
Nickel Alloy 600 and Inconel 600
Nickel Alloy 600 / Inconel 600: A nickel-chromium alloy with excellent resistance to high temperatures, oxidation, and corrosion. It is widely used in industries such as aerospace, chemical processing, and nuclear engineering.
Also, our company has other products, such as hastelloy, monel, incoloy, precision and titanium alloy.
Of course, the shape is optional, has bar, plate&sheet, coil, strip, tube&pipe, wire&mesh etc, or customerized goods.
Chemical Composition
Both Nickel 600 and Inconel Alloy 600 have the same chemical composition:
Element | Percentage |
---|---|
Nickel (Ni) | 72% min |
Chromium (Cr) | 14–17% |
Iron (Fe) | 6–10% |
Carbon (C) | 0.15% max |
Manganese (Mn) | 1% max |
Silicon (Si) | 0.5% max |
Copper (Cu) | 0.5% max |
Sulfur (S) | 0.015% max |
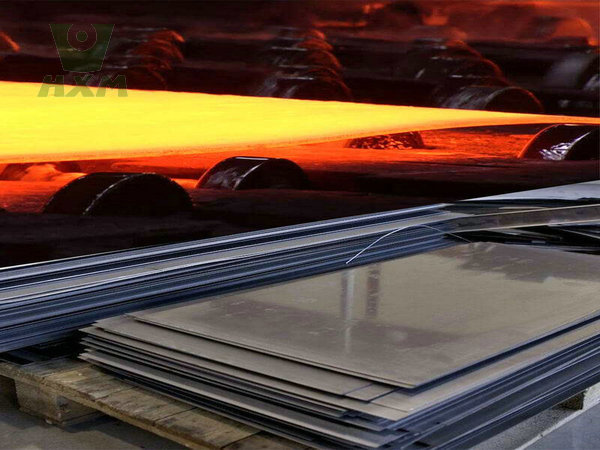
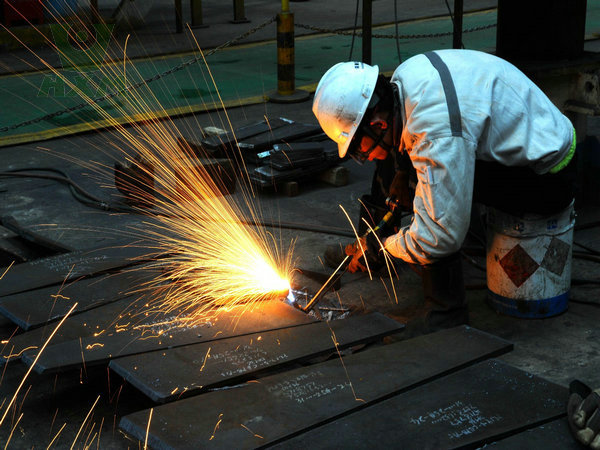
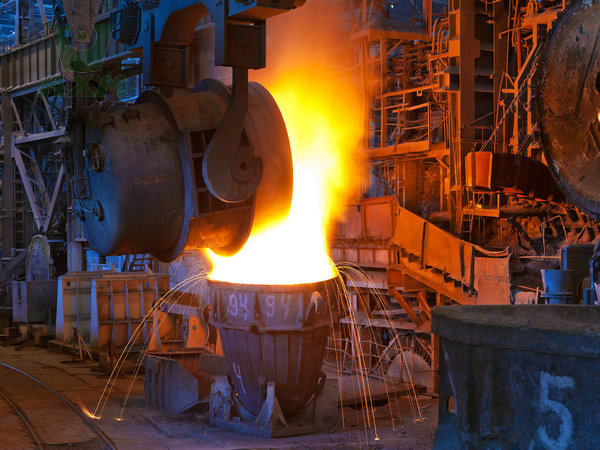
Mechanical Properties
The mechanical properties of Nickel 600 and Inconel Alloy 600 are identical:
Property | Value |
---|---|
Tensile Strength | 550–760 MPa (80–110 ksi) |
Yield Strength | 240–410 MPa (35–60 ksi) |
Elongation | 30–40% |
Hardness (Rockwell B) | 65–95 HRB |
Density | 8.47 g/cm³ (0.306 lb/in³) |
Melting Point | 1354–1413°C (2470–2580°F) |
Corrosion Resistance
Both materials exhibit excellent corrosion resistance due to their high nickel and chromium content:
Environment | Performance |
---|---|
Oxidizing Environments | Excellent resistance due to chromium. |
Reducing Environments | Good resistance, but not as strong as Hastelloy. |
High-Temperature Oxidation | Excellent resistance up to 1100°C (2012°F). |
Stress Corrosion Cracking (SCC) | Resistant in most environments, but susceptible in chloride-rich conditions. |
Inconel Alloy 600 Advantages and Limitations
Inconel Alloy 600 is a trademarked product of Special Metals Corporation, known for its stringent quality standards and consistency. Nickel Alloy 600, on the other hand, is a generic term and may be produced by various manufacturers, potentially leading to slight variations in quality. For industries where material consistency is critical, such as aerospace or nuclear engineering, the Inconel brand may be preferred despite its higher cost. Huaxiao Metal Manufacturer is professional and experienced in China, our company has over 10 years in alloy industry, which we are reliable and creditable, and our products are good quality in producing carefully to control quality. Service are personalized for every customer and providing the customerized solutions for the any problems.
Advantages | Limitations |
---|---|
– Excellent high-temperature strength. – Good oxidation and corrosion resistance. – Versatile in fabrication. | – Susceptible to stress corrosion cracking in chloride environments. – Expensive compared to stainless steels. – Difficult to machine and form. |

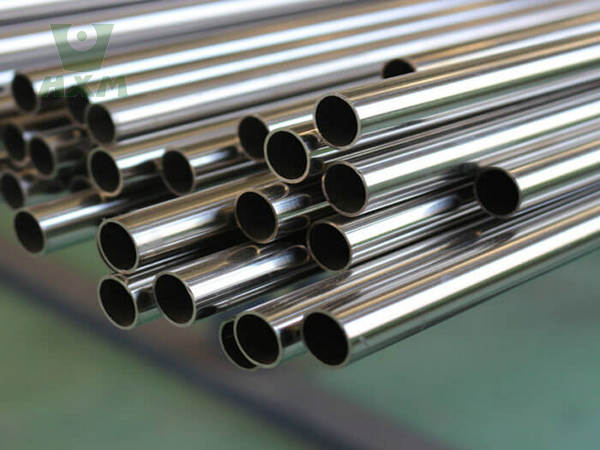
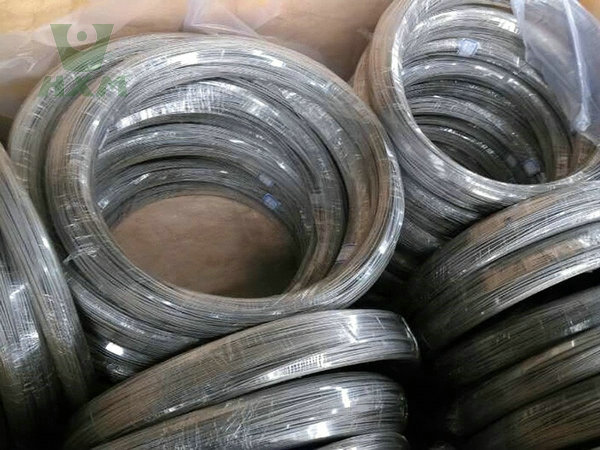
Fabrication Characteristics
Both materials share the same fabrication challenges and techniques:
Fabrication Process | Details | Challenges |
---|---|---|
Welding | – TIG, MIG, and SAW welding methods. – Use matching filler metals (e.g., ENiCrFe-3). | – Susceptibility to hot cracking. – Requires post-weld heat treatment for stress relief. |
Machining | – Use carbide or ceramic tools. – Slow speeds and high feed rates. – Coolants are essential. | – High work hardening tendency. – Tool wear due to toughness. |
Forming | – Cold forming for thin sections. – Hot forming at 870–1200°C (1600–2200°F). | – High strength makes forming difficult. – Risk of cracking during bending. |
Heat Treatment | – Solution annealing at 1010–1120°C (1850–2050°F). – Rapid cooling to prevent carbide precipitation. | – Overheating can cause grain growth. |
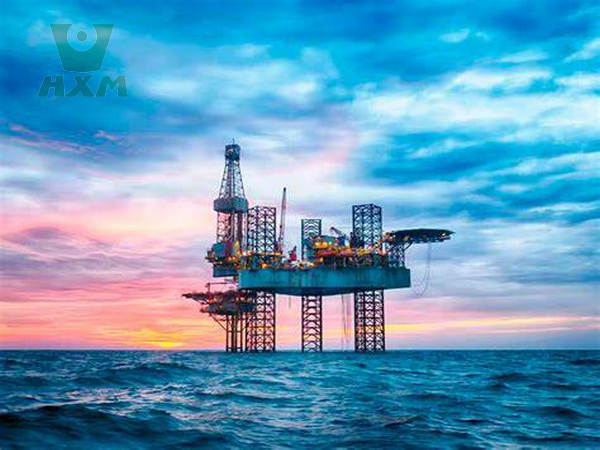
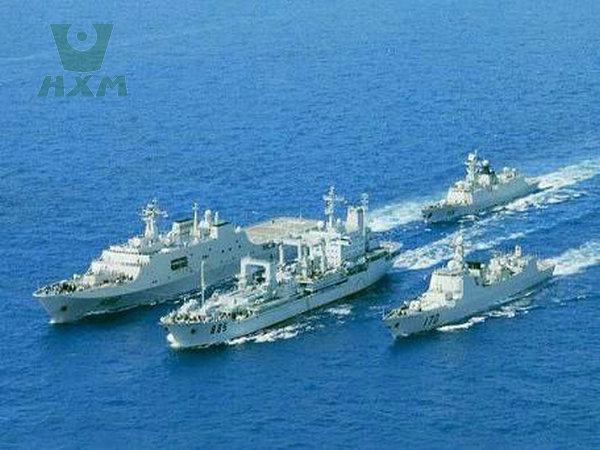
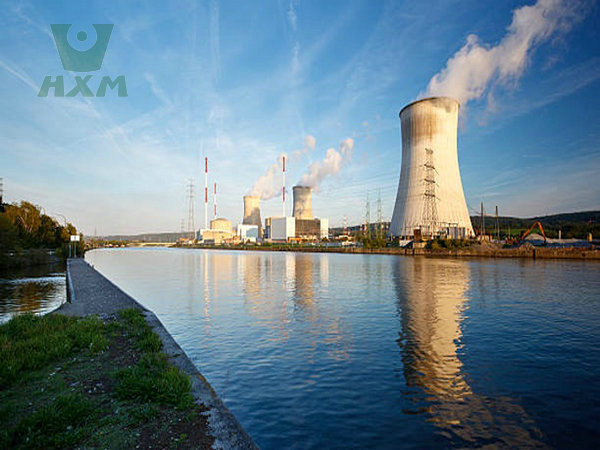
Inconel Alloy 600 and Nickel Alloy 600 Applications
Nickel 600 and Inconel Alloy 600 are used in similar applications due to their identical properties:
Industry | Applications |
---|---|
Aerospace | Turbine engines, exhaust systems. |
Chemical Processing | Reactors, heat exchangers, piping. |
Nuclear Engineering | Steam generator tubing, control rods. |
Heat Treating | Furnace components, muffles. |
Power Generation | Gas turbines, boiler components. |
Key Differences Between Nickel 600 and Inconel Alloy 600
Aspect | Nickel Alloy 600 | Inconel 600 |
---|---|---|
Name | Generic term for the alloy. | Trademarked name by Special Metals Corporation. |
Availability | Available from multiple manufacturers. | Specifically produced by Special Metals. |
Cost | Slightly lower due to generic branding. | Slightly higher due to brand premium. |
Quality Standards | May vary depending on the manufacturer. | Strict quality control under the Inconel brand. |
In Conclusion
Nickel 600 and Inconel Alloy 600 are essentially the same material, with identical chemical compositions, mechanical properties, and applications. The primary difference lies in the branding and quality control associated with the Inconel name. Both materials are highly valued for their corrosion resistance, high-temperature strength, and versatility in demanding environments. Huaxiao Metal Supplier has the complete system for customers to services for sale.
Nickel 600 and Inconel Alloy 600 are essentially the same material, offering exceptional performance in high-temperature and corrosive environments. Their widespread use in B2B applications across industries underscores their reliability and versatility. While the choice between the two often comes down to branding and quality assurance, both materials remain a cornerstone of modern engineering, providing solutions to some of the most challenging industrial problems. For businesses seeking high-performance materials, Nickel 600 and Inconel Alloy 600 are proven options that deliver long-term value and operational efficiency. If you have any qusestions , welcome to inquiry to our company.