Monel Metal, also known as Monel alloy, is a type of nickel-copper alloy that has been renowned for its exceptional properties since its inception. Developed by the International Nickel Company (INCO) in the early 20th century, Monel alloy was patented in 1906. This alloy is characterized by its strength and toughness over a wide temperature range, as well as its outstanding corrosion resistance.Huaxiao Metal Supplier provides all kinds of monel in the world for sale.
A family of nickel-chromium-molybdenum alloys (and sometimes including other elements such as cobalt, tungsten, and copper) designed for applications requiring excellent corrosion resistance, high temperature stability, and good mechanical properties. These alloys are widely used in the chemical processing, petrochemical, pollution control, pulp and paper, and aerospace industries, among others.
Monel Metal Overview
Monel Metal Alloy, a type of nickel-based alloy, is renowned for its excellent corrosion resistance, high-temperature strength, and good machinability. It primarily consists of nickel, cobalt, chromium, and other elements, which contribute to its unique properties. These alloys are categorized into various series such as K, R each with specific compositions and applications. Huaxiao Metal Supplier provides the various monel and the different shapes for customers.
Monel Metal Alloy Composition and Properties
Monel Metal is primarily a nickel-based Ni-Cu binary solid solution alloy. Nickel and copper can be infinitely miscible in any proportion, and due to the higher nickel content, Monel Metal maintains an austenitic single-phase structure over a wide temperature range. The copper nickel alloy content significantly enhances the alloy’s resistance to oxidation (corrosion) and provides good electrical conductivity. Additionally, microalloying elements such as aluminum and titanium play a role in age-hardening the alloy. Huaxiao Metal Supplier has the good quality monel alloy products.
Alloy Type | Composition (%) | Properties |
---|---|---|
Monel 400 | – Nickel (Ni): 63.0-70.0 (typically around 65%-70%), – Copper (Cu): 28.0-34.0 (typically around 28%-34%), – Iron (Fe): ≤2.5 (typically 2.0 max), – Manganese (Mn): 1.5-2.0, – Silicon (Si): ≤0.5, – Sulfur (S): ≤0.024 | – High corrosion resistance, especially in marine and chloride environments, – Good tensile strength and toughness, – Can be hardened only by cold working, – Melting point: 1300-1350°C<br> – Density: 8.80×103, – Non-toxic in solid form, but welding, grinding, or melting may produce hazardous fumes |
Monel K-500 | – Nickel (Ni): ≥63.0, – Copper (Cu): 27.0-33.0, – Iron (Fe): ≤2.0, – Manganese (Mn): ≤1.5, – Aluminum (Al): 2.3-3.15, – Titanium (Ti): 0.35-0.85, – Carbon (C): ≤0.25, – Silicon (Si): ≤0.5, – Sulfur (S): ≤0.01 | – Higher strength and hardness compared to Monel 400<br> – Excellent resistance to stress-corrosion cracking, – Good mechanical properties at elevated temperatures up to 600°C – Can be precipitation hardened for additional strength |
Monel alloy’s early applications were concentrated in the construction and home furnishing sectors. Notable examples include the use of nearly 120 tons of Monel sheet metal for the roof of Pennsylvania Station in New York in 1908. As its corrosion resistance became more apparent, Monel Metal alloy was increasingly adopted in buildings such as the Pentagon, the New York Historical Society Museum, and the Brooklyn Museum.
Beyond architectural applications, Monel alloy found its way into everyday life, particularly in food processing equipment due to its resistance to acidic foods and ease of cleaning. However, due to cost considerations, it was gradually replaced by austenitic stainless steel and Ni-Cr alloys in this sector.
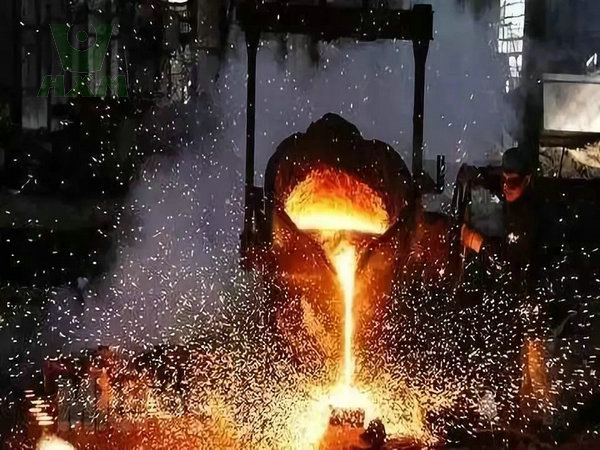
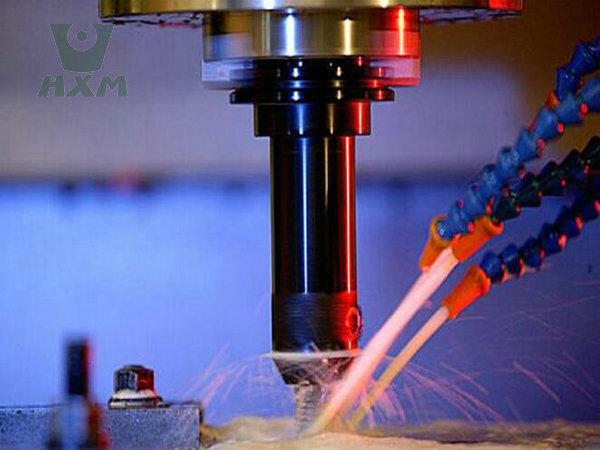
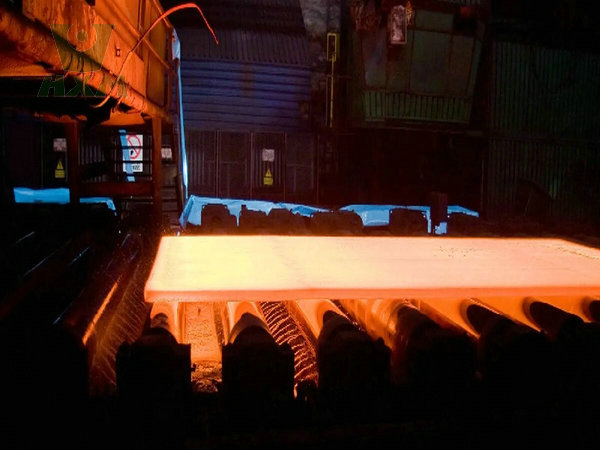
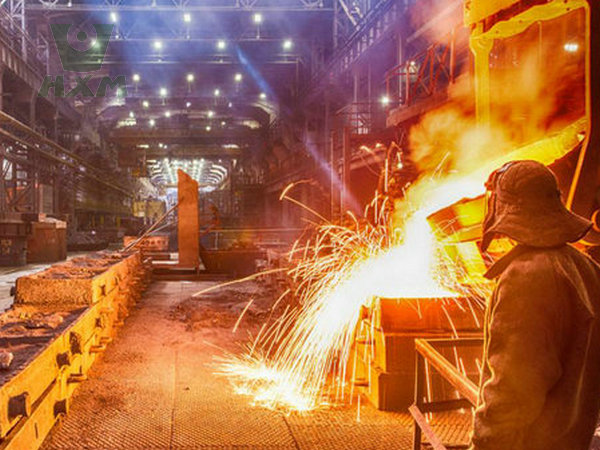
Military and Aerospace Applications
Monel alloy’s corrosion resistance in seawater quickly caught the attention of naval forces worldwide. The US Navy’s battleship North Dakota was the first to use Monel alloy propellers. During World War I, INCO supplied over 40 Monel Metal alloy propellers to the US Navy. Monel alloy components gained the trust of both the US and British navies due to their stable performance during the war and remain an important material choice for naval equipment to this day.
Types and Mechanical Properties
Monel alloys can be classified into solid solution-strengthened and precipitation-strengthened types based on their strengthening mechanisms. Solid solution-strengthened alloys, such as Monel 400, have good plasticity, making them suitable for marine applications like hulls or piping. Precipitation-strengthened alloys, like Monel K-500, have higher strength due to the formation of the γ’ phase during aging treatment and are used in components that require pressure resistance, such as fasteners in shipbuilding.
Monel Alloy History and Development
The story of Monel alloy begins with the efforts of D.H. Browne and Robert Crooks Stanley, metallurgists at INCO, who were working on optimizing the preparation process of German Silver (a Ni-Cu-Zn alloy). During their research, they stumbled upon a Ni-Cu intermediate alloy with a composition of approximately 70% nickel and 30% copper. This alloy exhibited a silver-white metallic luster, had a strength superior to ordinary steel of the time, and demonstrated better corrosion resistance than bronze in brine and sulfuric acid.
Recognizing the potential of this alloy, Stanley named it after Ambrose Monell, the then-president of INCO, in 1906 (omitting one ‘L’ because family names couldn’t be used as trademarks at that time). This led to the birth of Monel alloy, and Stanley’s role in INCO was subsequently solidified, eventually becoming its executive president in 1922.
Copper Nickel Alloy Application Analysis
Monel alloy exhibits good low-temperature toughness, with no ductile-brittle transition even at liquid hydrogen temperatures. It also has strong antioxidant capabilities in high-temperature environments and is resistant to combustion even in pure oxygen. Huaxiao Metal Manufacturer has the various alloy products and welcome to ask for the lastest price, which the price is suitable and afforable, if you have many of alloy, our company will you a cheap discount.
- Physical Appearance: Monel alloys have a gray, metallic luster.
- Hardness: Monel 400 typically has a hardness in the range of 110-150 HB.
- Thermal Conductivity: Monel alloys have a thermal conductivity of around 21.8 W/(m·K).
- Resistivity: The resistivity of Monel alloys is approximately 54.7×10^-8 ohm-m.
- Tensile Strength: Annealed Monel 400 has a tensile strength of 550 MPa.
- Modulus of Elasticity: The modulus of elasticity for Monel alloys is typically 179 GPa.
- Applications: Due to their corrosion resistance, tensile strength, and ability to withstand high temperatures, Monel alloys are widely used in marine environments, chemical processing equipment, aircraft components, heat exchangers, piping systems, and various other industries where corrosion resistance and high performance are critical.
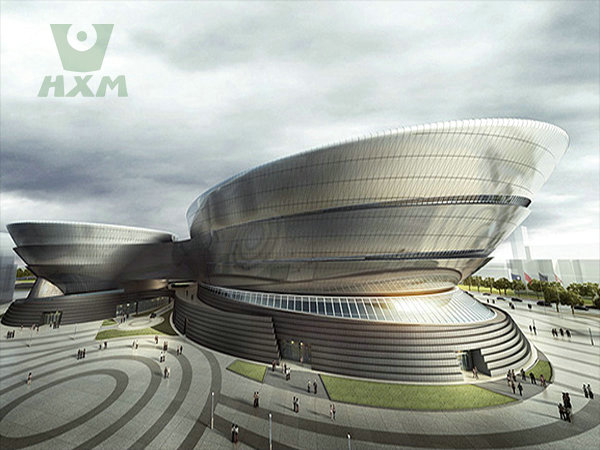
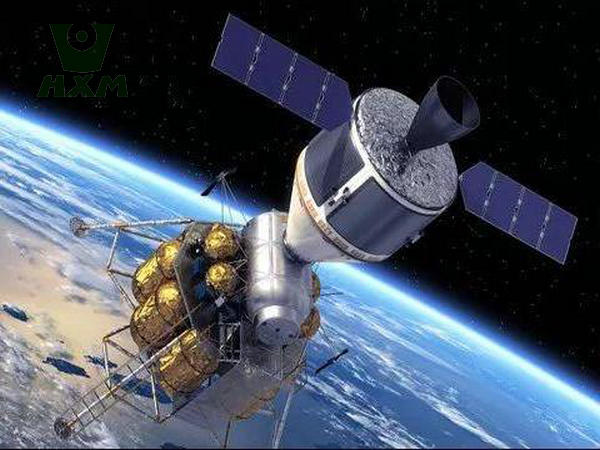
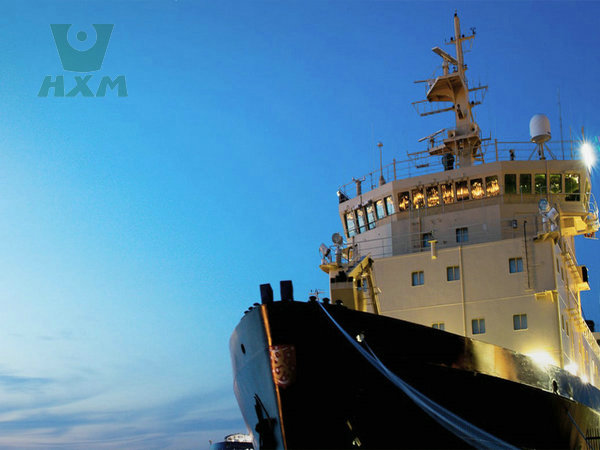

Copper Nickel Alloy Report Coverage
Monel alloy’s resistance to chloride stress corrosion cracking gave it an edge in other industries. It became a preferred material for components in the steel and petrochemical industries, such as pump shafts and industrial-grade pickling facilities. Its tolerance to halide salts and acids, including HCl and HF, made it ideal for use in containers, heat exchangers, and other equipment. The Copper Nickel Alloy has the good corrosion resiatant and durability.
Alloy Composition | Key Properties | Applications | Notes |
---|---|---|---|
90-10 Cu-Ni | – Excellent corrosion resistance in seawater<br>- Good biofouling resistance<br>- Cost-effective | – Offshore structures<br>- Condensers<br>- Piping systems<br>- Merchant shipping<br>- Naval vessels | Widely used due to balance of cost and performance |
70-30 Cu-Ni | – Higher strength than 90-10<br>- Better resistance to high seawater velocities<br>- Good corrosion resistance | – Desalination plants<br>- High-pressure piping<br>- Deep-sea applications | Used in more demanding environments |
Copper Nickel Alloy Research Methodology
This research methodology provides a structured approach to studying copper-nickel alloys, ensuring that all relevant properties and applications are considered. The specific data and tools used in each step contribute to a comprehensive understanding of these alloys. Copper Nickel alloy is a kind of metal materials with good performance, durability and wide application. Huaxiao Metal has the good copper nickel alloy as the top of distributer in China.
Research Step | Methodology | Specific Data/Tools Used | Description |
---|---|---|---|
1. Literature Review | Database Search | Scopus, Web of Science, Google Scholar | Collected and analyzed existing research papers, patents, and technical reports on copper-nickel alloys. |
Identified key properties, applications, and performance characteristics. | |||
2. Alloy Selection | Composition Analysis | Chemical composition tables, manufacturer specifications | Selected copper-nickel alloys based on desired properties (e.g., corrosion resistance, strength). |
Examples: Cu-10Ni, Cu-30Ni | Alloys with different nickel contents were chosen for comparison. | ||
3. Material Preparation | Casting/Forging | Melting furnace, forging press | Prepared alloy samples using casting or forging techniques. |
Heat Treatment | Furnace, quenching oil | Applied heat treatment to modify the microstructure and properties of the alloys. | |
4. Mechanical Testing | Tensile Testing | Universal testing machine | Measured tensile strength, yield strength, and elongation at break. |
Hardness Testing | Rockwell hardness tester | Determined the hardness of the alloys. | |
5. Corrosion Testing | Salt Spray Test | Salt spray chamber | Evaluated corrosion resistance by exposing samples to a salt spray environment. |
Immersion Test | Corrosive solutions (e.g., NaCl, H2SO4) | Assessed corrosion rates in different corrosive media. | |
6. Microstructural Analysis | Optical Microscopy | Optical microscope | Examined the microstructure of the alloys to understand the relationship between microstructure and properties. |
Scanning Electron Microscopy (SEM) | SEM | Provided detailed images of the alloy surface and fracture surfaces. | |
Energy Dispersive Spectroscopy (EDS) | EDS attachment on SEM | Analyzed the chemical composition of different phases within the alloy. | |
7. Data Analysis | Statistical Analysis | Software (e.g., SPSS, Excel) | Analyzed and interpreted the experimental data using statistical methods. |
Correlation Analysis | Scatter plots, regression analysis | Assessed the correlation between alloy composition, microstructure, and mechanical/corrosion properties. | |
8. Reporting | Technical Report | Word processing software (e.g., Microsoft Word) | Prepared a detailed technical report summarizing the research methodology, results, and conclusions. |
In Conclusion
The Monel alloy market is a dynamic and growing sector with significant potential for expansion. The increasing demand from various industries, technological advancements, and expanding application scope are driving the market. However, manufacturers need to address challenges such as high production costs and complex manufacturing processes to remain competitive. Copper Nickel Alloy is monel alloy and the chararistics is good performance and wide practicality. Huaxiao Metal Supplier provides the excellent alloy products, if you have any questions about alloy, please contact us or send the email to our experts, who will slove your problem and offer the customrized solutions for you. Looking forward to your consultation and informations to us in web or email.
Copper-nickel alloys offer a balance of corrosion resistance, strength, and cost-effectiveness that makes them ideal for a wide range of marine and industrial applications. The detailed analysis and table provided in this report offer insights into the properties and applications of these alloys, helping to inform decision-making in material selection and design. By focusing on innovation, cost reduction, and expanding their geographical reach, manufacturers can capitalize on the market opportunities and drive growth. Monel alloy’s unique combination of strength, toughness, and corrosion resistance has made it an indispensable material in various high-risk and high-demand fields such as shipbuilding, aerospace, and military applications. Its irreplaceable properties ensure its continued use in critical applications.