Titanium alloy manufacturers are a highly specialized and technologically advanced industry. The production of titanium alloys involves complex processes, including extraction, refining, alloying, and fabrication. The industry is characterized by high costs, stringent quality requirements, and significant applications in aerospace, medical, and industrial sectors.Titanium alloy manufacturers play a crucial role in various industries due to the unique properties of titanium alloys, such as high strength, low density, corrosion resistance, and good biocompatibility.
Below is a detailed analysis of titanium alloy manufacturers, covering various aspects such as production processes, market trends, key players, and challenges.
Titanium Alloy is one of the most widely used titanium alloys in the aerospace, medical, and industrial sectors. It is an alpha-beta alloy, composed primarily of titanium, aluminum, and vanadium. This alloy is renowned for its excellent strength-to-weight ratio, corrosion resistance, and biocompatibility.
Huaxiao Metal Supplier has the various titanium alloy and the quality is good in China.
Titanium Alloy manufacturers, has revolutionized the manufacturing industry by enabling the creation of complex structures with high precision. Among the various materials used in 3D printing, titanium alloy stands out due to its exceptional properties. This report delves into the intricacies of 3D printing titanium alloy, analyzing its characteristics, advantages, applications, and comparing it with other materials.
Titanium Alloy Production Processes
Titanium alloy manufacturing involves several critical steps:
Extraction: Titanium is extracted from ores like ilmenite and rutile using the Kroll process or the Hunter process.
Refining: The extracted titanium is purified to produce titanium sponge.
Alloying: Titanium is combined with other elements (e.g., aluminum, vanadium) to create alloys with enhanced properties.
Fabrication: The alloys are processed into various forms (e.g., sheets, bars, tubes) through forging, rolling, or casting.
Comparison: Traditional methods like the Kroll process are energy-intensive and costly, while newer methods like the FFC Cambridge process aim to reduce costs and environmental impact.
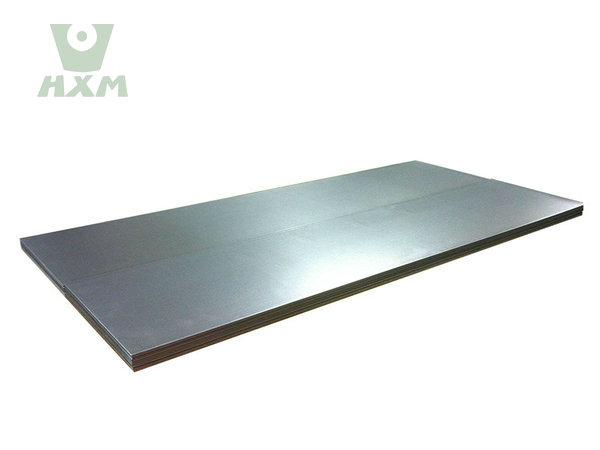
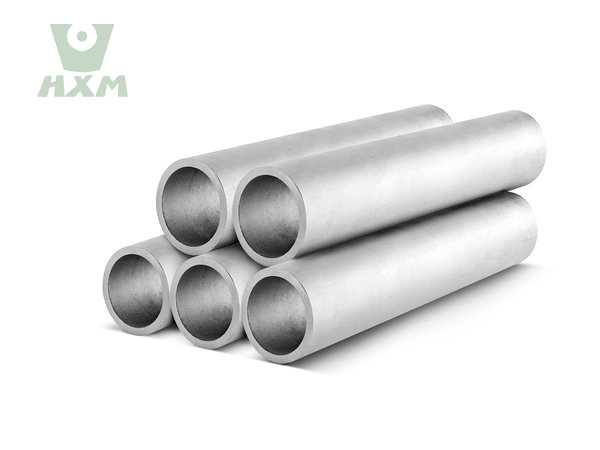
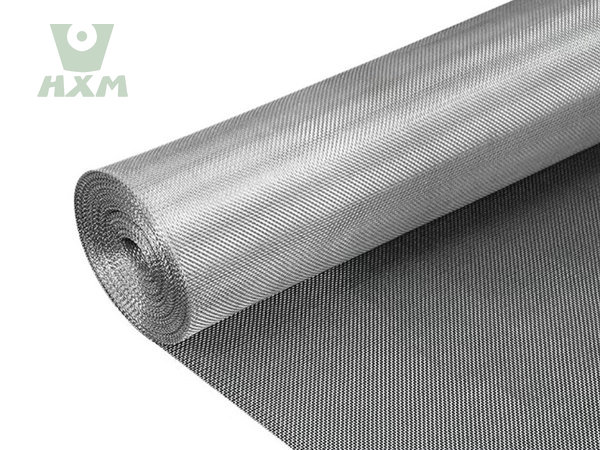
Titanium Alloy Market Trends
The global titanium alloy manufacturers are driven by demand from aerospace, medical, and automotive industries.
Aerospace: Titanium alloys are widely used in aircraft engines and airframes due to their high strength-to-weight ratio and corrosion resistance.
Medical: Titanium alloys are used in implants and surgical instruments because of their biocompatibility.
Automotive: The automotive industry is increasingly using titanium alloys to reduce vehicle weight and improve fuel efficiency.
Titanium Alloy Manufacturers Data
The global titanium alloy market was valued at 5.2billionin2022∗∗andisprojectedtoreach∗∗5.2billionin2022∗∗andisprojectedtoreach∗∗8.1 billion by 2030, growing at a CAGR of 5.7%.
Aerospace accounts for 50% of titanium alloy consumption, followed by industrial applications (25%) and medical (15%).
Titanium Alloy Key Players
The titanium alloy manufacturing industry is dominated by a few major players, with significant competition from regional manufacturers.
Company | Country | Market Share | Key Products |
---|---|---|---|
VSMPO-AVISMA | Russia | 30% | Titanium ingots, sheets, forgings |
TIMET (Titanium Metals Corporation) | USA | 20% | Titanium alloys for aerospace |
ATI (Allegheny Technologies) | USA | 15% | Specialty titanium alloys |
Baoji Titanium Industry | China | 10% | Low-cost titanium products |
Precision Castparts Corp | USA | 10% | Titanium castings for aerospace |
Comparison: VSMPO-AVISMA dominates the market due to its large-scale production capabilities, while Chinese manufacturers like Baoji Titanium Industry are gaining market share by offering cost-competitive products.
Huaxiao Metal titanium alloy Manufacturers also provides other shapes of Titanium Alloy products, such as plate&sheet, bar, coil,wire&mesh, tube&pipe, strip. The price is affordable and suitable.
Benefits of Using Titanium Alloy Manufacturers
Advantage | Description |
---|---|
Design Freedom | Enables the creation of complex geometries that are impossible with traditional methods. |
Lightweight and Strong | Titanium’s high strength-to-weight ratio is perfect for aerospace and automotive industries. |
Material Efficiency | Reduces waste by using only the required amount of material. |
Customization | Allows for tailored designs to meet specific application requirements. |
Rapid Prototyping | Speeds up the development process by quickly producing prototypes. |
Cost-Effective for Small Batches | Eliminates the need for expensive molds or tooling for small production runs. |
Advantages and Performance Comparison
1. High Strength and Low Density
Titanium alloy manufacturers offer a high strength-to-density ratio, enabling the production of lightweight yet strong components. This is particularly advantageous in aerospace applications where weight reduction is crucial for fuel efficiency.
Comparison with Aluminum:
- Titanium alloy manufacturers have a higher strength-to-density ratio than aluminum, making it more suitable for high-load applications.
- Aluminum, while lighter, has lower strength and may not be suitable for extreme environments.
2. Excellent Corrosion Resistance
Titanium alloy exhibits exceptional corrosion resistance in various environments, including acidic, alkaline, and seawater. This makes it ideal for use in marine applications and chemical processing equipment.
Comparison with Stainless Steel:
- Titanium alloy has superior corrosion resistance to stainless steel in many environments.
- Stainless steel may corrode in certain aggressive chemicals or high-temperature conditions.
3. Good Biocompatibility
Titanium alloy’s biocompatibility makes it an excellent choice for medical implants such as artificial joints and dental implants. Its use in medical applications ensures long-term durability and reduces the risk of complications.
4. High-temperature Performance
Titanium alloy can operate at temperatures up to 500°C, making it suitable for high-temperature applications such as aerospace engines and gas turbines.
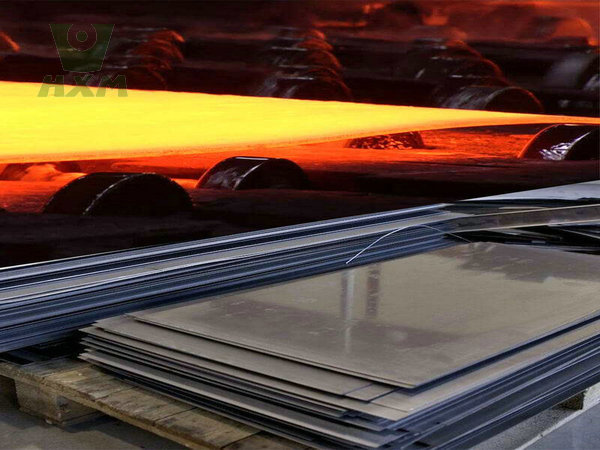
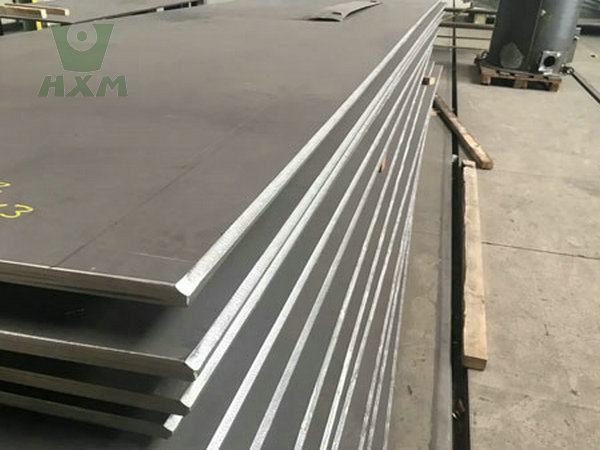
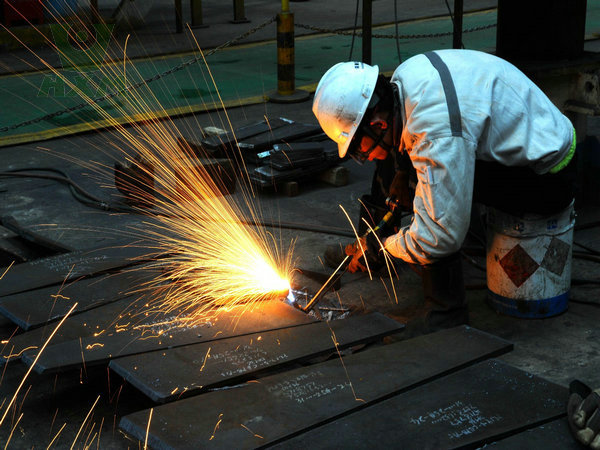
Huaxiao Metal Supplier provides all kinds of titanium alloy products in the world. Welcome to inquiry and ask for the lastest price. Looking forward to your email, which I am convienced that you will be satisfied to our products.
Titanium Alloy Manufacturers Challenges
Titanium alloy manufacturers face several challenges:
High Costs: The extraction and processing of titanium are expensive, making titanium alloys costly compared to alternatives like aluminum or steel.
Supply Chain Issues: The industry relies on a few suppliers for raw materials, leading to supply chain vulnerabilities.
Environmental Concerns: Traditional titanium production methods are energy-intensive and generate significant waste.
Example: The Kroll process consumes 10-15 times more energy than aluminum production, making sustainability a major concern. Titanium alloy manufacturers have the fast delievery around the world.
Huaxiao Metal Supplier provides professional services and reasonable prices, offering customers the best quality products. The Titanium Alloy Factory is a specialized manufacturing facility dedicated to the production of high-quality titanium alloy. This factory combines advanced technology, rigorous quality control, and experienced personnel to ensure the production of titaium alloy the highest standards.The factory is equipped with state-of-the-art production equipment and machinery, capable of producing titanium alloy with precise dimensions and consistent quality.Welcome to reqiure, and ask to the lastest price list.
Titanium Alloy Manufacturers
- Manufacturing Processes: Ti-6Al-4V can be processed using various methods, including forging, casting, machining, and additive manufacturing (3D printing).
Cost: The cost of Ti-6Al-4V is relatively high due to the expensive raw materials and complex processing required. However, its superior properties often justify the cost in critical applications.
Alloy Type | Applications | Examples |
---|---|---|
CPTi | Orthopedic implants | Bicon®, Allofit®, TOP acetabular cup system® |
Ti-6Al-4V | Aerospace, Medical, Marine | Engine parts, hip replacements, ship propellers |
Ti-Al-Nb | Orthopedic implants | Various cementless prosthesis components |
- Raw Materials: The cost of titanium sponge, the primary raw material for producing Ti-6Al-4V, can fluctuate due to market conditions and supply chain disruptions. Cost reduction strategies include using low-cost raw materials like titanium hydride powder and recycling scrap material.
- Processing Techniques: Various manufacturing techniques can be used to produce Ti-6Al-4V components, including casting, forging, extrusion, rolling, and powder metallurgy. Each technique has its own cost implications and is suitable for specific applications.
- Heat Treatment: Heat treatment can optimize the mechanical properties of Ti-6Al-4V by reducing residual stresses and improving ductility and toughness. This process adds to the overall cost but is essential for achieving the desired material properties.
- Precision Machining: High-precision machining is often required to achieve the tight tolerances and complex geometries required for aerospace and medical applications. This adds to the cost but ensures the production of high-quality components.
Titanium Alloy Innovations and Future Outlook
To address challenges, manufacturers are investing in research and development:
Additive Manufacturing: 3D printing of titanium alloys is gaining traction, especially in the aerospace and medical sectors.
Sustainable Processes: New methods like the FFC Cambridge process aim to reduce energy consumption and waste.
Alloy Development: Advanced titanium alloys with improved properties (e.g., higher temperature resistance) are being developed for next-generation applications.
Data:
The additive manufacturing market for titanium alloys is expected to grow at a CAGR of 20% from 2022 to 2030.
Investments in R&D for titanium alloys have increased by 15% annually over the past five years.
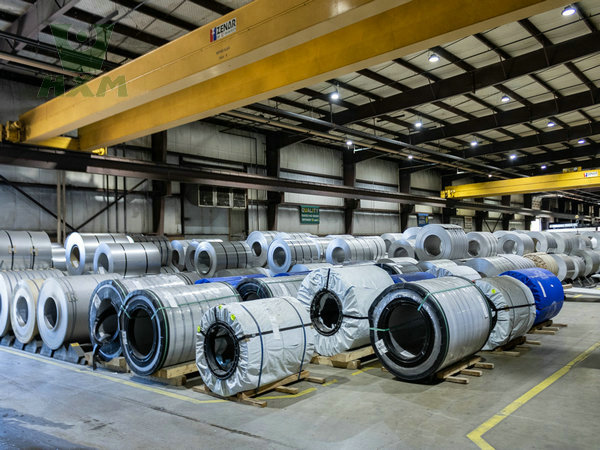
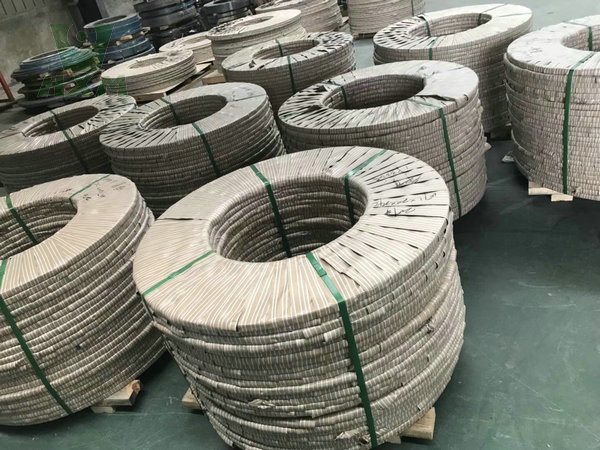
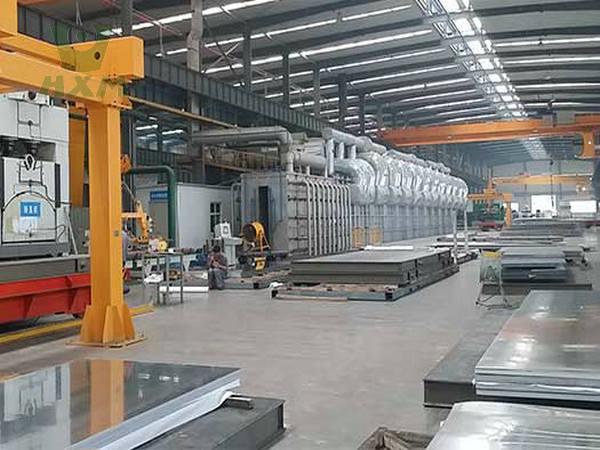
Titanium Alloy Regional Analysis
The titanium alloy manufacturers industry is geographically concentrated, with key regions including:
North America: Dominated by the aerospace industry, with major players like TIMET and ATI.
Europe: Strong demand from the automotive and medical sectors, with companies like VSMPO-AVISMA supplying the region.
Asia-Pacific: Rapid growth driven by China and India, with increasing demand from industrial and aerospace sectors.
Comparison: North America and Europe focus on high-end applications, while Asia-Pacific emphasizes cost-effective production. Titanium alloy manufacturers have the various titanium alloy in China.
Titanium Alloy Cost Analysis
The cost structure of titanium alloy manufacturers are influenced by raw materials, energy, and labor.
Cost Component | Percentage of Total Cost |
---|---|
Raw Materials | 40% |
Energy | 30% |
Labor | 15% |
Equipment | 10% |
Others | 5% |
Example: Titanium alloy manufacturers the cost of titanium sponge, a key raw material, accounts for 40-50% of the total production cost.
Applications of Titanium Alloy in Various Industries
1. Aerospace
Titanium alloy is extensively used in aerospace applications due to its combination of high strength, low density, and corrosion resistance. 3D printing enables the manufacturing of complex components like aircraft engine parts and structural frames with enhanced performance and reliability.
2. Medical
In the medical field, 3D printed titanium alloy is used to create highly personalized implants that match the patient’s bone structure. This results in better fit, reduced complications, and longer implant lifespan.
3. Automotive
The automotive industry leverages 3D printed titanium alloy to create lightweight components such as engine brackets and suspension systems, improving fuel efficiency and performance while reducing emissions and noise levels.
4. Energy
Titanium alloy is also used in the production of key components for efficient energy equipment, such as gas turbine blades and wind turbine components, contributing to the sustainable development of the energy industry.
Titanium alloy manufacturers must adhere to strict quality standards, especially for aerospace and medical applications.
Aerospace: Standards like AMS (Aerospace Material Specifications) and ASTM (American Society for Testing and Materials) are mandatory.
Medical: ISO 13485 certification is required for titanium alloys used in medical devices.
Comparison: Aerospace-grade titanium alloys require higher purity and stricter quality control compared to industrial-grade alloys.
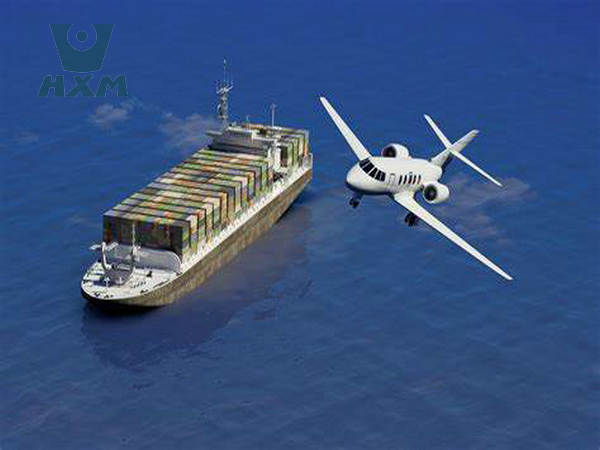
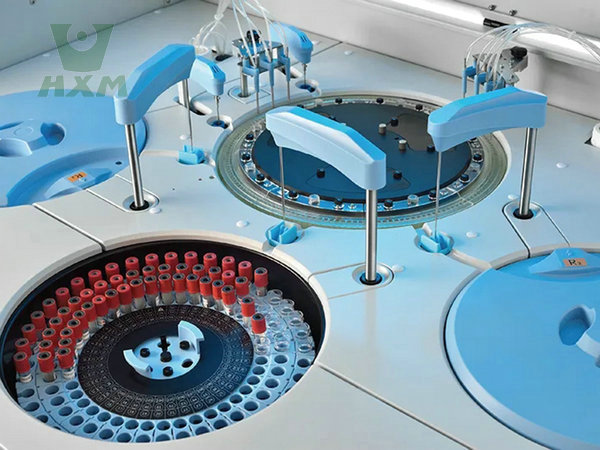
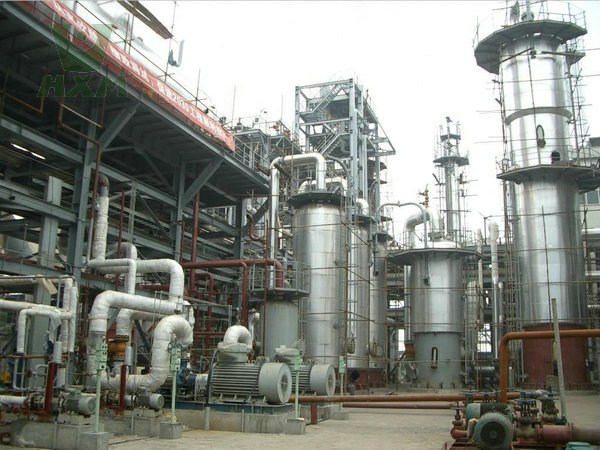
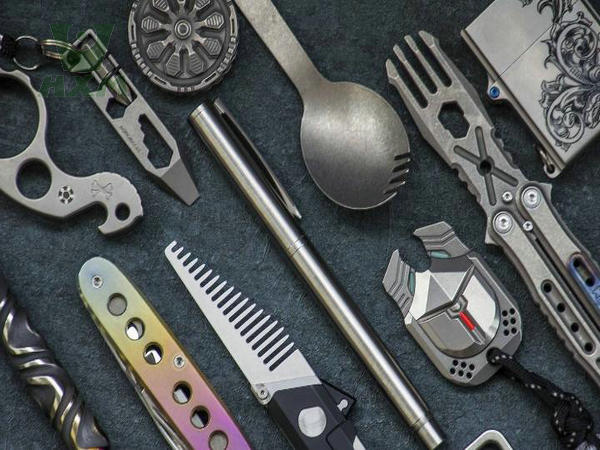
In Conclusion
Titanium alloy manufacturers are a critical industry with significant growth potential. While the industry faces challenges like high costs and environmental concerns, innovations in production processes and applications are driving its evolution. Key players like VSMPO-AVISMA and TIMET dominate the market, but regional manufacturers in Asia-Pacific are gaining traction. Our products are guaranteed in quality, and our professional team can provide technical support and consulting services. If you need more information or have any questions, please free to contact our customer service team.
The future of titanium alloy manufacturers lies in sustainable practices, advanced alloys, and additive. Huaxiao Metal Supplier is professional and experienced in alloy producing factory, our company provides the personalized services and welcome to inquiry about the lastest price. Titanium alloy manufacturers are diverse, with various processes, product types, and applications. They face unique challenges but continue to innovate and improve quality control measures. The global market for titanium alloys is growing, driven by demand from industries like aerospace, medical, and marine. By adhering to strict standards and focusing on sustainability, titanium alloy manufacturers are poised for continued success and growth.
Aspect | Details |
---|---|
Market Size (2022) | $5.2 billion |
Projected Market (2030) | $8.1 billion |
Key Applications | Aerospace (50%), Industrial (25%), Medical (15%) |
Major Players | VSMPO-AVISMA, TIMET, ATI, Baoji Titanium Industry |
Key Challenges | High costs, supply chain issues, environmental concerns |
Innovations | Additive manufacturing, sustainable processes, advanced alloys |
Regional Focus | North America (aerospace), Asia-Pacific (cost-effective production) |